Aerosol Deposition Method –ADM - Les avantages
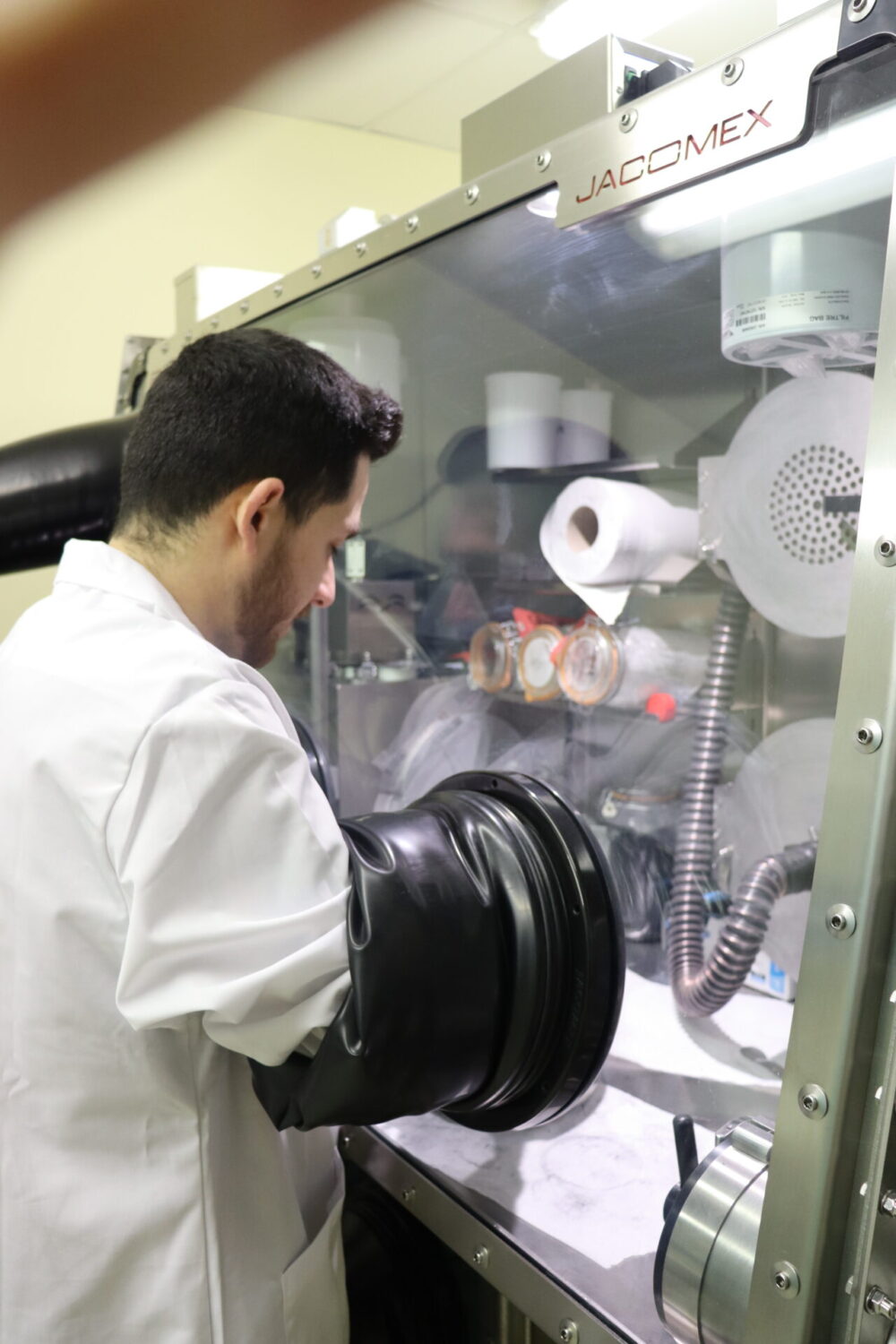
26 Fév 25
Articles
Temps de lecture : 16 minutes
Notre série d'articles sur l'Aerosol Deposition Method continue. Après un article général, cette semaine nous vous proposons de lever le voile sur les avantages de l'ADM.
L’Aerosol Deposition Method (ADM) est une technique innovante de formation de revêtements céramiques (mais aussi parfois métalliques) à température ambiante. Cette technologie se caractérise principalement par la formation de revêtements denses (> 95%), nanostructurés et d’épaisseur micrométrique [1].
L’ADM a été développé dans les années 1990 au Japon. La formation des revêtements exploite principalement la plasticité des particules céramiques à l’échelle submicrométrique/nanométrique. Ce phénomène se manifeste également dans les métaux sous forme de déformation localisée amplifiée. Pour ce faire, des particules sèches fines (submicrométriques à quelques micromètres) sont accélérées à des vitesses entre 100–600 m/s jusqu’à impacter un substrat. L’énergie cinétique de ces particules favorise leur déformation, leur fragmentation et la formation de surfaces hautement réactives qui conduisent à la consolidation et la densification de couches sur un substrat sans apport de chaleur, contrairement aux procédés traditionnels basés sur l’énergie thermique [1–3].
Les avantages principaux de l'ADM
Efficacité énergétique
En exploitant exclusivement l’énergie cinétique, l’ADM fonctionne à température ambiante, éliminant le besoin de chauffage ou de consolidation thermique. La consommation d’énergie est considérablement réduite par rapport aux méthodes de frittage traditionnel et aux procédés de formation de dépôts telle que le dépôt physique en phase vapeur (PVD), le dépôt chimique en phase vapeur (CVD), la projection thermique ou les procédés en phase liquide. Cette efficacité énergétique plus importante résulte dans une diminution de la consommation énergétique estimée entre 50 et 82% [4].
Conditions de vide minimales
L'ADM se distingue par sa capacité à opérer à pression quasi-atmosphérique ou en conditions de vide brut (1 mbar ou légèrement inférieure), sans nécessiter de vide poussé ou ultra-poussé. Cette simplicité opératoire en fait une solution accessible, économiquement avantageuse et aisément adaptable à des environnements industriels variés, contrairement aux procédés en phase vapeur, qui nécessitent des infrastructures complexes et coûteuses pour atteindre ces niveaux de vide nécessaires [5].
Consommation réduite et faible pression des gaz
L’ADM utilise des pressions de gaz proches de la pression atmosphérique (< 2,5 bars), limitant la consommation de ressources et simplifiant le dimensionnement des équipements. À l’inverse, des procédés comme le Cold Spray nécessitent des pressions très élevées (jusqu’à 50 bars), des températures pouvant atteindre 1100°C et une consommation importante de gaz comprimé ou inerte, augmentant les coûts opérationnels et logistiques [5].
Préservation des priorités des matériaux natifs et substrats
Grâce à l’absence de hautes températures, l’ADM conserve l’intégrité chimique, cristallographique et microstructurale des matériaux déposés. Cette préservation est particulièrement bénéfique par rapport aux matériaux qui peuvent voir leurs propriétés dégradées par les procédés thermiques conventionnels. L’ADM permet de déposer des revêtements ayant des propriétés spécifiques et fonctionnelles telle que la résistance à la corrosion, la résistance à l’usure, une bonne conductivité électrique, ainsi des propriétés piézoélectriques et optiques. De plus, ce procédé permet de traiter une grande variété de substrats, y compris des matériaux fragiles, sans risque de chocs thermiques ou de déformations [6].
Densification et consolidation immédiate
L’ADM permet d’obtenir des revêtements densifiés (> 95% de la densité théorique) dès leur réalisation, sans nécessiter de post étape de consolidation thermique. Cette densité élevée assure des propriétés mécaniques optimales et des performances fonctionnelles supérieures à de nombreux autres procédés, souvent limités par une densification insuffisante. De plus, pour certains matériaux, surtout composites, la densité peut être modulée dans une certaine mesure. Cette modulation, bien que limitée, ouvre des possibilités pour des applications nécessitant une porosité contrôlée ou des propriétés particulières [7].
Cinétique de croissance de dépôt modérée
L’ADM offre une cinétique de croissance de dépôt (entre 0,1 et 10 µm/min), généralement supérieure à celle des procédés en phase vapeur, qui peuvent atteindre seulement quelques nanomètres par minute, mais inférieure à celle de la projection thermique, capable de produire des dépôts épais en quelques secondes.
Polyvalence des substrats et d’épaisseur
L’ADM offre une flexibilité unique, permettant le dépôt sur des substrats variés tels que les métaux, les polymères, les céramiques et les composites. Elle est également adaptée aux substrats flexibles ou faible épaisseur (> 80 µm), et permet de moduler les épaisseurs des revêtements entre des couches fines (≳ 0,7 µm) et des couches épaisses (> 100 µm et ≲ 500µm) pour répondre à des besoins fonctionnels et protecteurs divers.
Polyvalence technologique
S’approchant des principes phénoménologiques bien compris et largement étudiés des procédés de projection thermique, l’ADM est une technologie qui peut être facilement combinée avec ces procédés afin d’exploiter ses avantages intrinsèques, d’améliorer la qualité et le rendement de la formation du revêtement ainsi que d’élargir les possibilités en termes d’épaisseur [4]. Cela constitue un domaine actif de recherche du CTTC en collaboration avec l’Institut de Recherche sur les Céramiques –IRCER [8].
Respect de l’environnement
Sans besoin de gaz comprimés à haute pression ni de chaleur excessive, l’ADM présente une empreinte carbone réduite et minimise les émissions de gaz à effet de serre. Par rapport aux procédés en phase vapeur ou thermiques utilisant des produits chimiques toxiques ou polluants, le procédé ADM constitue une technologie écoresponsable répondant aux exigences croissantes en matière de durabilité industrielle.
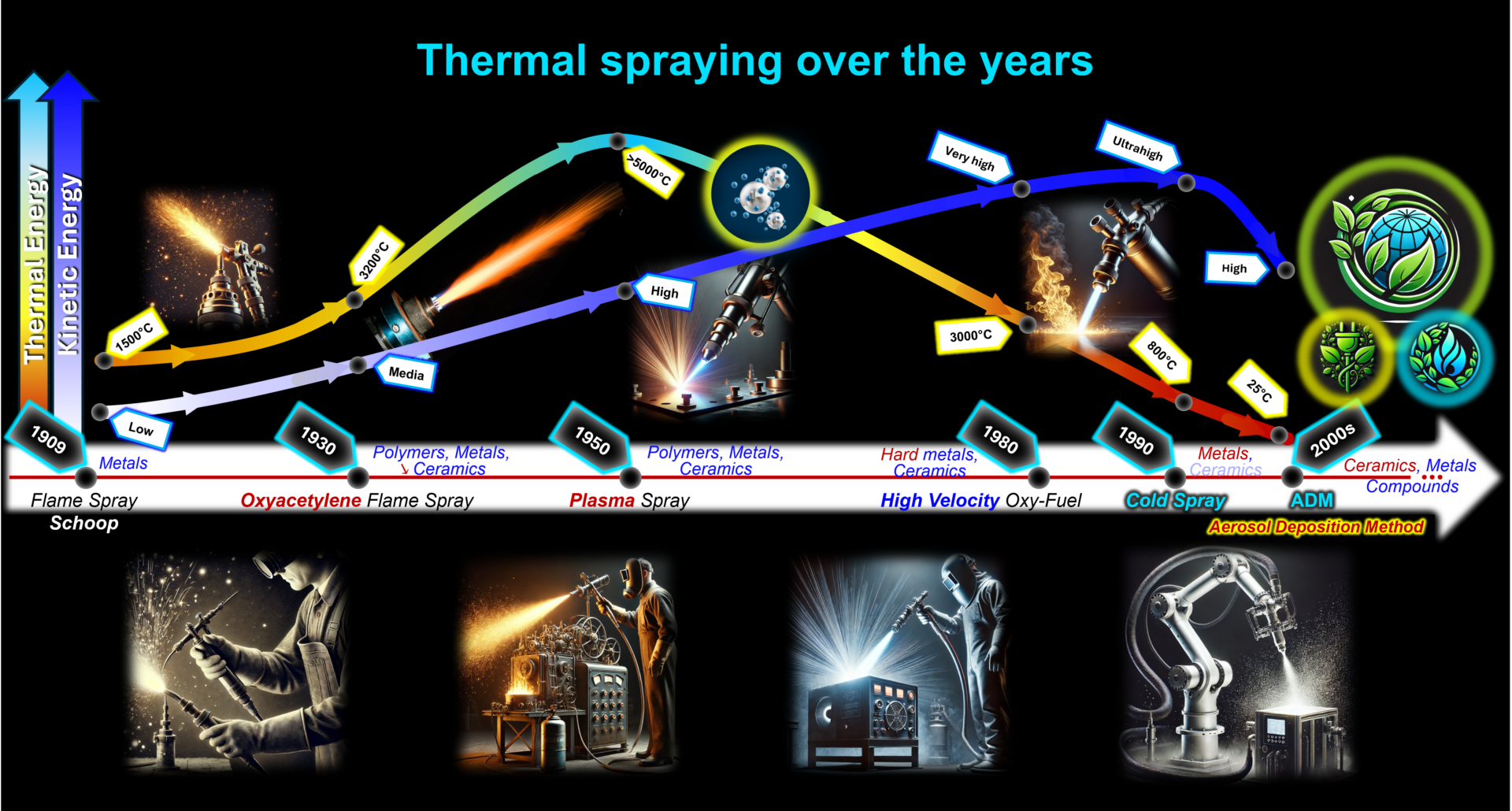
Nos articles sur l'ADM
Références Bibliographiques
[1] J. Akedo, Aerosol deposition of ceramic thick films at room temperature: Densification mechanism of ceramic layers, in: Journal of the American Ceramic Society, 2006: pp. 1834–1839. https://doi.org/10.1111/j.1551-2916.2006.01030.x.
[2] D. Hanft, J. Exner, M. Schubert, T. Stöcker, P. Fuierer, R. Moos, An overview of the Aerosol Deposition method: Process fundamentals and new trends in materials applications, Journal of Ceramic Science and Technology 6 (2015) 147–181. https://doi.org/10.4416/JCST2015-00018.
[3] J. Akedo, Room temperature impact consolidation and application to ceramic coatings: Aerosol deposition method, Journal of the Ceramic Society of Japan 128 (2020) 101–116. https://doi.org/10.2109/jcersj2.19196.
[4] K. Shinoda, H. Noda, K. Ohtomi, T. Yamada, J. Akedo, Promotion of knowledge and technology transfer towards innovative manufacturing process: Case study of new hybrid coating process, International Journal of Automation Technology 13 (2019) 419–431. https://doi.org/10.20965/ijat.2019.p0419.
[5] A. Vardelle, C. Moreau, J. Akedo, H. Ashrafizadeh, C.C. Berndt, J.O. Berghaus, M. Boulos, J. Brogan, A.C. Bourtsalas, A. Dolatabadi, M. Dorfman, T.J. Eden, P. Fauchais, G. Fisher, F. Gaertner, M. Gindrat, R. Henne, M. Hyland, E. Irissou, E.H. Jordan, K.A. Khor, A. Killinger, Y.C. Lau, C.J. Li, L. Li, J. Longtin, N. Markocsan, P.J. Masset, J. Matejicek, G. Mauer, A. McDonald, J. Mostaghimi, S. Sampath, G. Schiller, K. Shinoda, M.F. Smith, A.A. Syed, N.J. Themelis, F.L. Toma, J.P. Trelles, R. Vassen, P. Vuoristo, The 2016 Thermal Spray Roadmap, Journal of Thermal Spray Technology 25 (2016) 1376–1440. https://doi.org/10.1007/s11666-016-0473-x.
[6] C. Lee, M.Y. Cho, M. Kim, J. Jang, Y. Oh, K. Oh, S. Kim, B. Park, B. Kim, S.M. Koo, J.M. Oh, D. Lee, Applicability of Aerosol Deposition Process for flexible electronic device and determining the Film Formation Mechanism with Cushioning Effects, Sci Rep 9 (2019). https://doi.org/10.1038/s41598-019-38477-y.
[7] J. Akedo, Room temperature impact consolidation (RTIC) of fine ceramic powder by aerosol deposition method and applications to microdevices, Journal of Thermal Spray Technology 17 (2008) 181–198. https://doi.org/10.1007/s11666-008-9163-7.
[8] M. Shahien, M. Suzuki, K. Shinoda, J. Akedo, Ceramic Coatings Deposited from Fine Particles by Different Spraying Processes, Journal of Thermal Spray Technology 29 (2020) 2033–2047. https://doi.org/10.1007/s11666-020-01095-6.