L'Aerosol Deposition Method (ADM)
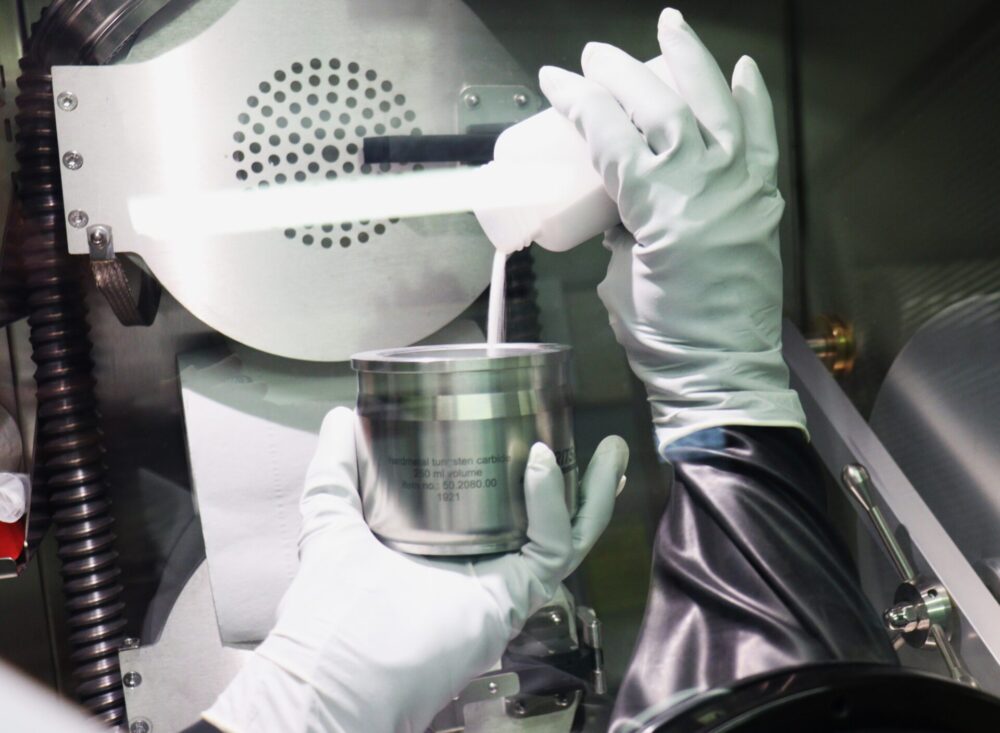
22 Jan 25
Articles
Temps de lecture : 16 minutes
L'Aerosol Deposition Method (ADM) est une technologie innovante pour des revêtements céramiques à faible impact environnemental
Revêtements et ingénierie de surfaces : une introduction vers l’Aerosol Deposition Method
Les revêtements céramiques : un pilier pour les matériaux performants
Les revêtements jouent un rôle crucial dans l’amélioration des propriétés des matériaux et des surfaces. Ils répondent à des exigences de performance élevées dans des environnements souvent extrêmes. En particulier, les revêtements céramiques grâce à leurs propriétés exceptionnelles permettent d’obtenir des solutions adaptées aux environnements les plus exigeants. Cela passe par des améliorations des propriétés mécaniques, thermiques et chimiques. Dans des secteurs tels que l’aéronautique, l’énergie ou l’industrie médicale, ils permettent de protéger les surfaces contre l’usure, la corrosion ou la chaleur. Ils confèrent également des fonctionnalités spécifiques. Ces couches sont souvent déterminantes pour garantir la performance et la durabilité des pièces.
Évolution des technologies de dépôt : vers des solutions écologiques et performantes
Pour répondre à ces besoins, différentes technologies de dépôt ont été développées au fil du temps. Les procédés en phase vapeur, bien que précis, nécessitent des infrastructures coûteuses et des conditions de vide poussé et même ultra-poussé (>10-8 mbar). Les procédés en phase liquide, plus simples, sont limités par la faible densité des dépôts et sont énergivores. Ces limitations ont contribué à faire de la projection thermique l’une des techniques les plus utilisées. Elle est appréciée pour sa polyvalence et ses performances dans de nombreuses applications industrielles. Toutefois, même au sein de cette technologie, des alternatives ont émergé pour relever les défis énergétiques et élargir les champs d’application.
Depuis son invention en 1909 par Schoop, principalement pour le dépôt de métaux, la projection thermique a progressivement évolué. Elle permet désormais le dépôt de céramiques et de composites en exploitant des sources d’énergie comme le plasma ou les arcs électriques. Cette technologie a transformé la fabrication de revêtements en combinant polyvalence et performance. Cependant, elle repose toujours sur des apports énergétiques élevés. La chaleur nécessaire à la fusion ou semi-fusion des particules entraîne une consommation importante de ressources. Elle provoque souvent, des altérations chimiques et structurales des matériaux, compromettant leurs propriétés fonctionnelles. Avec le temps, des efforts ont été faits pour réduire cette dépendance à l’énergie thermique, favorisant l’énergie cinétique. Cela a donné naissance à des technologies comme le Cold Spray. Cette méthode minimise les dégradations thermiques en projetant des particules à grande vitesse sans les fondre. Pour atteindre ces vitesses élevées, il est cependant nécessaire de recourir à des pressions très élevées et à une consommation importante de gaz. De plus, cette méthode reste limitée aux matériaux ductiles, laissant les céramiques pures en marge de ces avancées. Cependant, elles peuvent être co-déposées avec des métaux, comme cela se fait depuis peu (cf. Figure 1).
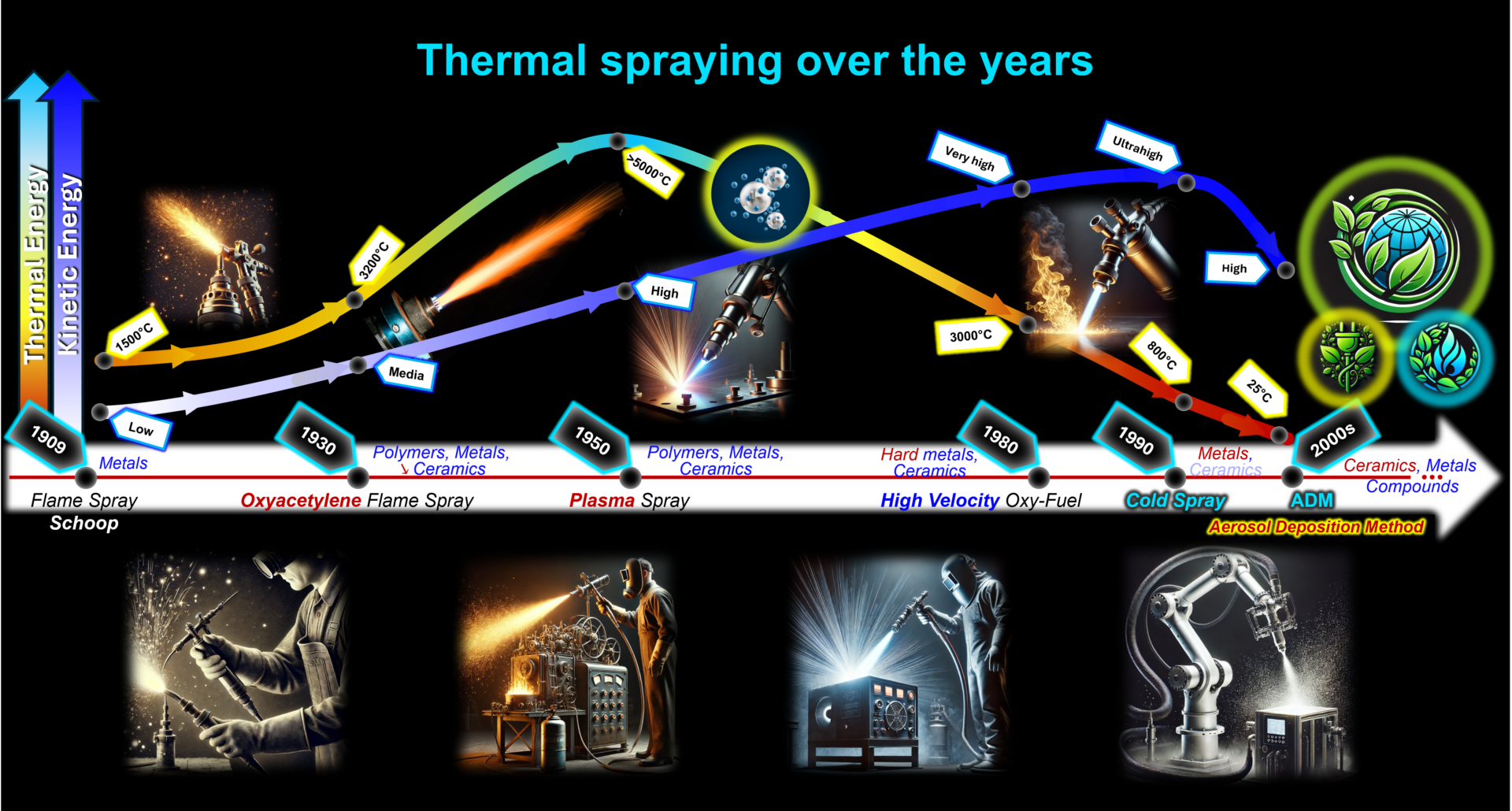
L’évolution des besoins industriels et les contraintes environnementales appellent aujourd’hui à repenser les technologies de revêtement. Il s'agit de réduire la consommation énergétique, l’empreinte carbone et l’utilisation de gaz tout en maintenant des performances élevées. La technologie Aerosol Deposition Method (ADM), bien que récente, s’impose progressivement comme une solution prometteuse. Exploitant exclusivement l’énergie cinétique, elle permet le dépôt de céramiques, de composites et même de métaux à température ambiante. Cela s'applique sur une large gamme de substrats (rigides, flexibles, minces ou épais), tout en évitant ainsi les contraintes thermiques tout en offrant une alternative simple, efficace et respectueuse de l’environnement.
Comment intégrer l'ADM aux technologies existantes
L’ADM, en tant que méthode innovante, ne vise pas seulement à remplacer certaines applications des technologies existantes. Elle peut aussi s’y intégrer en tant que complément, offrant des solutions hybrides adaptées à des problématiques complexes. L’ADM s’inscrit dans l'héritage des progrès phénoménologiques et technologiques de la projection thermique. Elle s'affranchit des contraintes énergétiques et environnementales, ouvrant ainsi la voie à de nouvelles opportunités industrielles.
Qu’est-ce que l’ADM ?
L’Aerosol Deposition Method (ADM) est une technique novatrice de dépôt de revêtements. Elle se caractérise principalement par la formation de films denses (>95%) et nanostructurés directement à température ambiante. Contrairement aux procédés traditionnels basés sur l’énergie thermique, l’ADM exploite exclusivement l’énergie cinétique pour consolider les particules. Elle ne nécessite ni fusion ni recuit, préservant ainsi les propriétés intrinsèques des matériaux déposés.
Cette méthode utilise des particules solides sèches en suspension dans un gaz porteur sec (air comprimé, O2, N2, He, Ar… ou mélanges). Elle repose sur l’impact à haute vitesse (100–600 m/s) de ces particules sur un substrat. Cela entraîne une série de phénomènes mécaniques complexes tels que la déformation plastique, la fissuration et la fragmentation. À l’échelle nanométrique, les céramiques exhibent une pseudo-plasticité facilitant leur déformation sous contraintes. Les métaux, naturellement ductiles, subissent des déformations mécaniques amplifiées par ces mêmes contraintes. Ces mécanismes conduisent à la création de nouvelles surfaces hautement réactives. Ensemble, elles favorisent l’adhésion, la consolidation et la densification des couches composant le revêtement en cours de formation.
Les origines
L’ADM est né dans les années 1990 au Japon. Des chercheurs, en s’appuyant sur des avancées en physique des solides, ont exploré la plasticité à l’échelle submicrométrique/nanométrique des céramiques. Ce phénomène se manifeste également dans les métaux sous forme de déformation localisée amplifiée. Cette découverte a ouvert la voie à une méthode capable de déposer des céramiques, mais aussi des métaux et composites. Ces composites incluent les céramique-métaux et céramique-polymère)adaptés à une grande variété de substrats.
Les avantages principaux de l’ADM incluent :
✔️ Efficacité énergétique : en exploitant exclusivement l’énergie cinétique, l’ADM fonctionne à température ambiante, éliminant le besoin de chauffage ou de consolidation thermique. Cela réduit considérablement la consommation d’énergie par rapport à la projection thermique ou les procédés en phase liquide.
✔️ Conditions de vide minimales : l’ADM se distingue par sa capacité à opérer à pression quasi-atmosphérique ou en conditions de vide brut (1 mbar ou légèrement inférieur), sans nécessiter de vide poussé/ultra-poussé. Cette simplicité opératoire en fait une solution accessible, économiquement avantageuse et aisément adaptable à des environnements industriels variés, contrairement aux procédés en phase vapeur, qui nécessitent des infrastructures complexes et coûteuses pour atteindre les niveaux de vide nécessaires.
✔️ Consommation réduite et faible pression des gaz : l’ADM utilise des pressions de gaz proches de la pression atmosphérique (< 2,5 bar), limitant la consommation de ressources et simplifiant le dimensionnement des équipements. À l’inverse, des procédés comme le Cold Spray nécessitent des pressions très élevées (jusqu’à 50 bar), des températures pouvant atteindre 1100°C et une consommation importante de gaz comprimé ou inerte, augmentant les coûts opérationnels et logistiques.
✔️ Préservation des propriétés des matériaux et des substrats : grâce à l’absence de hautes températures, l’ADM conserve l’intégrité chimique, cristallographique et microstructurale des matériaux déposés. Cette préservation est particulièrement bénéfique par rapport aux matériaux qui peuvent être dégradés par les procédés thermiques. De plus, l’ADM permet de traiter une grande variété de substrats, y compris des matériaux fragiles, sans risque de déformation thermique.
✔️ Densification et consolidation immédiate : l’ADM permet d’obtenir des revêtements densifiés (> 95% de la densité théorique) dès leur application, sans nécessiter d’étape de consolidation thermique. Cette densité élevée assure des propriétés mécaniques optimales et des performances fonctionnelles supérieures à de nombreux autres procédés, souvent limités par une densification insuffisante. De plus, pour certains matériaux, surtout composites, la densité peut être modulée dans une certaine mesure. Cette flexibilité, bien que limitée, ouvre des possibilités pour des applications nécessitant une porosité contrôlée ou des propriétés spécifiques.
✔️ Cinétique de croissance de dépôt modérée : l’ADM offre une cinétique de croissance de dépôt (entre 0,1 et 10 µm/min), généralement supérieure à celle des procédés en phase vapeur, qui peuvent atteindre seulement quelques nanomètres par minute, mais inférieure à celle de la projection thermique, capable de produire des dépôts épais en quelques secondes.
✔️ Polyvalence des substrats et d’épaisseur : l’ADM offre une flexibilité unique, permettant le dépôt sur des substrats variés tels que les métaux, les polymères, les céramiques et les composites. Elle est également adaptée aux substrats flexibles ou faible épaisseur (> 80 µm), et permet de moduler les épaisseurs des revêtements entre des couches fines (≳ 0,7 µm) et des couches épaisses (> 100 µm et ≲ 500µm) pour répondre à des besoins fonctionnels et protecteurs divers.
✔️ Respect de l’environnement : sans besoin de gaz comprimés à haute pression ni de chaleur excessive, l’ADM présente une empreinte carbone réduite et minimise les émissions de gaz à effet de serre. Par rapport aux procédés en phase vapeur ou thermiques, elle constitue une technologie écoresponsable répondant aux exigences croissantes en matière de durabilité industrielle.
Le dispositif ADM
Le dispositif ADM (cf. Figure 2) se compose principalement de trois éléments : un générateur d’aérosol (AG), une chambre de dépôt (CR) et un système de pompage. Le processus débute par la formation d’un aérosol dans l’AG, où des particules sèches sont mises en suspension grâce à l’injection d’un gaz porteur (par exemple, N₂, He, Ar, Air comprimé sec) et un effet vibratoire. La différence de pression de vide entre l’AG et la CR permet le transport des particules à travers une buse, où elles sont accélérées avant d’être projetées sur le substrat pour former le dépôt. L’absence de frittage ou de traitement thermique postérieur réduit la consommation d’énergie tout en minimisant l’impact environnemental.
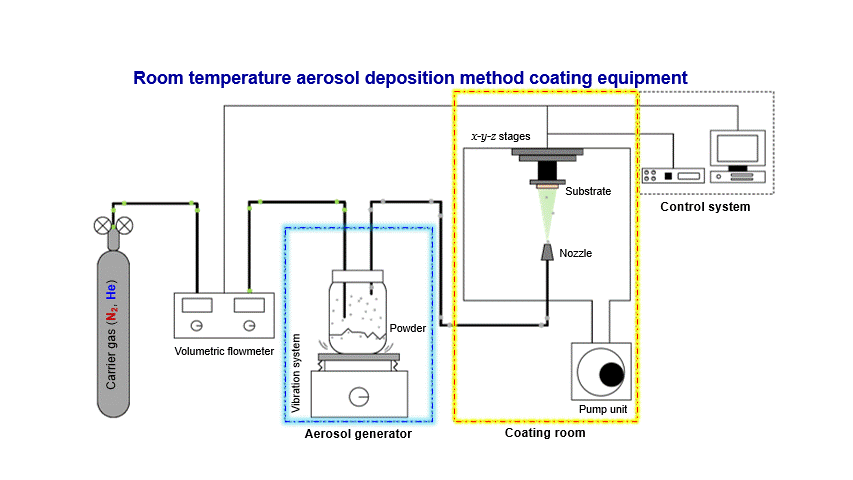
Principes fondamentaux de la formation de revêtements par AD
Phénomènes Physico-chimiques de l’ADM
L’Aerosol Deposition Method (ADM) repose sur des phénomènes physico-chimiques complexes permettant de consolider des particules céramiques à température ambiante. Ce processus, décrit par Jun Akedo sous le concept de Room Temperature Impact Consolidation (RTIC), est largement reconnu par la communauté scientifique. Grâce à de nombreuses études et à l’expertise du CTTC, une séquence chronologique des étapes clés a été établie, allant de la génération de l’aérosol à la formation du revêtement.
✔️ Génération et Accélération des Particules : les particules céramiques, de tailles comprises entre 0,1 et 5 µm, sont mises en suspension dans un gaz porteur sous faible pression (0,1–0,25 MPa), formant un aérosol stable. Ces particules, propulsées à travers une buse supersonique, atteignent des vitesses allant de 100 à 600 m/s, accumulant une énergie cinétique suffisante pour initier la consolidation lors de leur impact avec le substrat.
✔️ Impact Initial sur le Substrat : lors de l’impact, les particules exercent des pressions locales très élevées, entre 1 et 15 GPa, pendant quelques nanosecondes. Ces contraintes provoquent une fragmentation rapide des particules, générant des fragments nanométriques dotés de surfaces réactives et de liaisons libres, augmentant ainsi leur énergie de surface. En parallèle, l’impact entraîne une érosion du substrat, créant une rugosité locale qui favorise l’adhérence mécanique.
✔️ Plasmas Locaux et Fracto-émission : l’impact des particules à haute vitesse provoque la fragmentation et l’érosion du substrat, rompant des liaisons chimiques et libérant électrons, ions et nanoparticules réactives. Ces phénomènes peuvent conduire à la formation de plasmas transitoires, susceptibles d’activer chimiquement les surfaces et de favoriser l’adhésion initiale. Bien que leur rôle exact dans l’ADM soit encore peu étudié, ils représentent un domaine actif de recherche où le CTTC contribue significativement à approfondir la compréhension de ces mécanismes complexes, en collaboration avec l’Institut de Recherche sur les Céramiques.
Formation du Revêtement et Densification
✔️ Libération et Dissipation de l’Énergie Thermique : une partie de l’énergie cinétique des particules est convertie en chaleur transitoire lors de l’impact, entraînant une élévation thermique locale qui peut atteindre 200 à 500°C. Bien que cette chaleur locale soit rapidement dissipée, elle contribue à activer les surfaces et à améliorer l’adhérence. Dans le cas des substrats métalliques, comme l’aluminium, cette énergie thermique peut également provoquer des microdéformations localisées, renforçant l’ancrage mécanique.
✔️ Fragments Nanométriques et Interaction avec le Substrat : les fragments résiduels issus de la fragmentation des particules se réorganisent pour maximiser les contacts interparticulaires et améliorer la cohésion locale. La compatibilité chimique entre les fragments et le substrat favorise la formation de liaisons chimiques initiales, renforçant l’adhérence. Ces liaisons, souvent iono-covalentes dans le cas des céramiques, assurent une cohésion essentielle pour les étapes suivantes de densification.
✔️ Formation de la Première Couche : les fragments générés lors de l’impact interagissent chimiquement et physiquement avec le substrat pour former une première couche d’une épaisseur inférieure à 1 µm. Ce processus repose sur un pseudo-frittage (consolidation), où les liaisons réactives (Van der Waals, ioniques et/ou covalentes) entre les fragments et le substrat assurent une consolidation initiale. Cette couche joue un rôle de stabilisation, agissant comme un tampon pour les impacts suivants et facilitant la progression uniforme du revêtement.
✔️ Martelage et Densification : les impacts successifs des particules exercent une pression supplémentaire sur le revêtement, réduisant progressivement la porosité initiale à moins de 5%, atteignant une densité relative supérieure à 95%. Ce processus est soutenu par la pseudo-plasticité des céramiques à l’échelle nanométrique, tandis que dans les métaux, la déformation plastique contribue à une meilleure compaction.
✔️ Construction Multicouches : chaque nouvelle couche déposée interagit mécaniquement avec les couches précédentes, influençant la structure globale du revêtement. Ce processus permet d’atteindre des épaisseurs contrôlées allant de 1 à 500 µm, adaptées à des applications spécifiques telles que les barrières thermiques, les couches protectrices ou les matériaux fonctionnels pour l’électronique et l’optique
Importance des matières premières et des paramètres cinétiques
Préparation des Matières Premières et Contrôle des Paramètres Cinétiques
Le succès de l’Aerosol Deposition Method (ADM) repose sur une préparation rigoureuse et un contrôle précis des matières premières ainsi que des paramètres cinétiques. Ces facteurs, qui constituent l’élément clé du processus, déterminent directement la qualité du dépôt et l’efficacité globale du procédé. C’est pourquoi le CTTC, fort de plus de 40 ans d’expérience dans le travail des céramiques et l’adaptation des matières premières, a concentré ses efforts sur cet aspect. Grâce à l’expertise développée depuis plusieurs années sur le traitement des matières premières pour l’ADM, il a pu développer des matériaux adaptés, permettant non seulement de former des revêtements de haute qualité, mais aussi d’en moduler l’épaisseur pour répondre à des besoins spécifiques.
Facteurs clés de la production de revêtements de haute qualité
✔️ Taille des particules. La distribution granulométrique est un paramètre clé pour garantir une projection stable et une consolidation efficace (cf. Figure 3) :
- Particules fines : en raison de leur faible inertie, elles ont tendance à rebondir sur le substrat, diminuant ainsi l’efficacité du dépôt.
- Particules grossières : elles peuvent provoquer une érosion excessive du substrat et limiter la densification du revêtement.
- Distribution contrôlée : une granulométrie optimisée, entre 0,1 et 5 µm, permet d’équilibrer inertie et énergie cinétique pour maximiser l’adhésion et réduire les pertes/l’érosion.
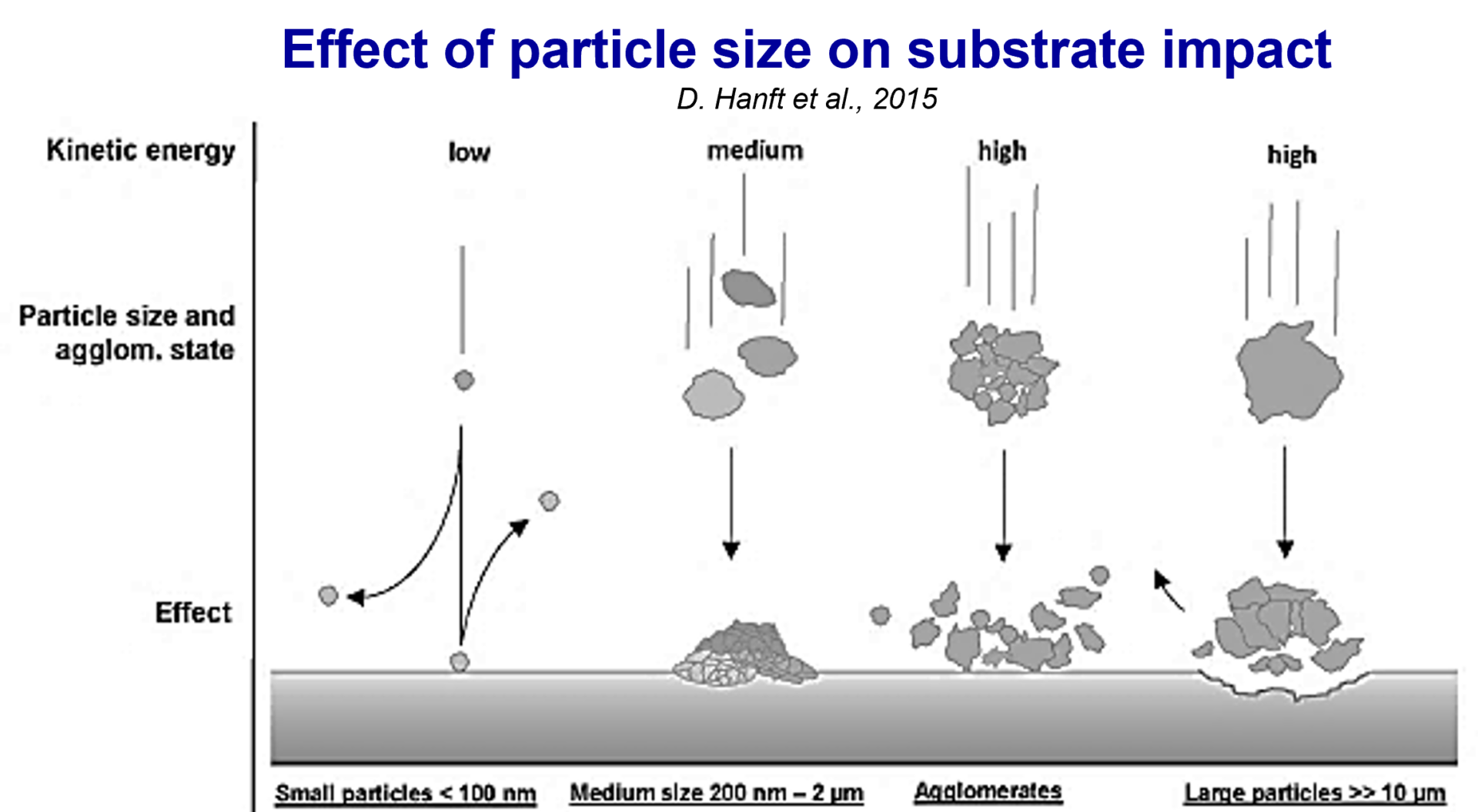
Référence bibliographique :
D. Hanft, J. Exner, M. Schubert, T. Stöcker, P. Fuierer, R. Moos, An Overview of the Aerosol Deposition Method: Process Fundamentals and New Trends in Materials Applications, Journal of Ceramic Science and Technology 6 (2015) 147–182.
✔️ Morphologie des particules : les particules sphériques ou isotropes favorisent une trajectoire stable et une dispersion homogène dans le flux gazeux (cf. Figure 4). Des traitements peuvent être appliqués pour stabiliser son comportement aérodynamique.
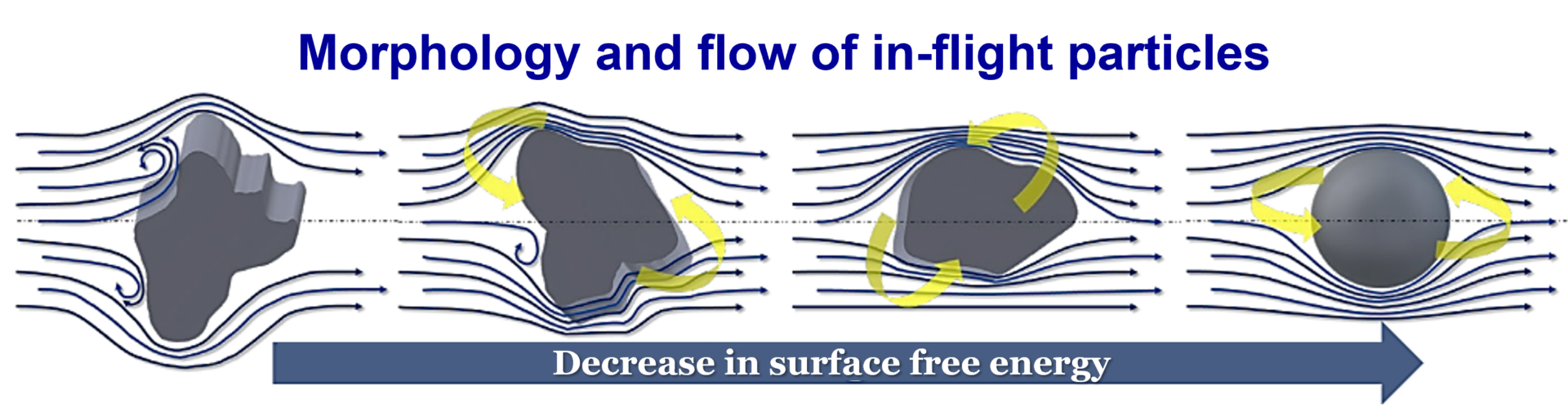
Référence bibliographique
Contribution à la compréhension de la formation de la porosité dans des revêtements et des particules de verre bioactif élaborés par projection thermique pour des applications biomédicales, Université de Limoges / Universidad de Antioquia, 2021.
✔️ Vitesse critique et paramètres cinétiques : chaque matériau et taille de particule possède une vitesse critique spécifique qui influence directement la fragmentation et la consolidation. Une vitesse insuffisante peut limiter l’adhésion, tandis qu’une vitesse excessive peut entraîner une érosion accrue ou une dégradation de la structure du substrat (cf. Figure 5).
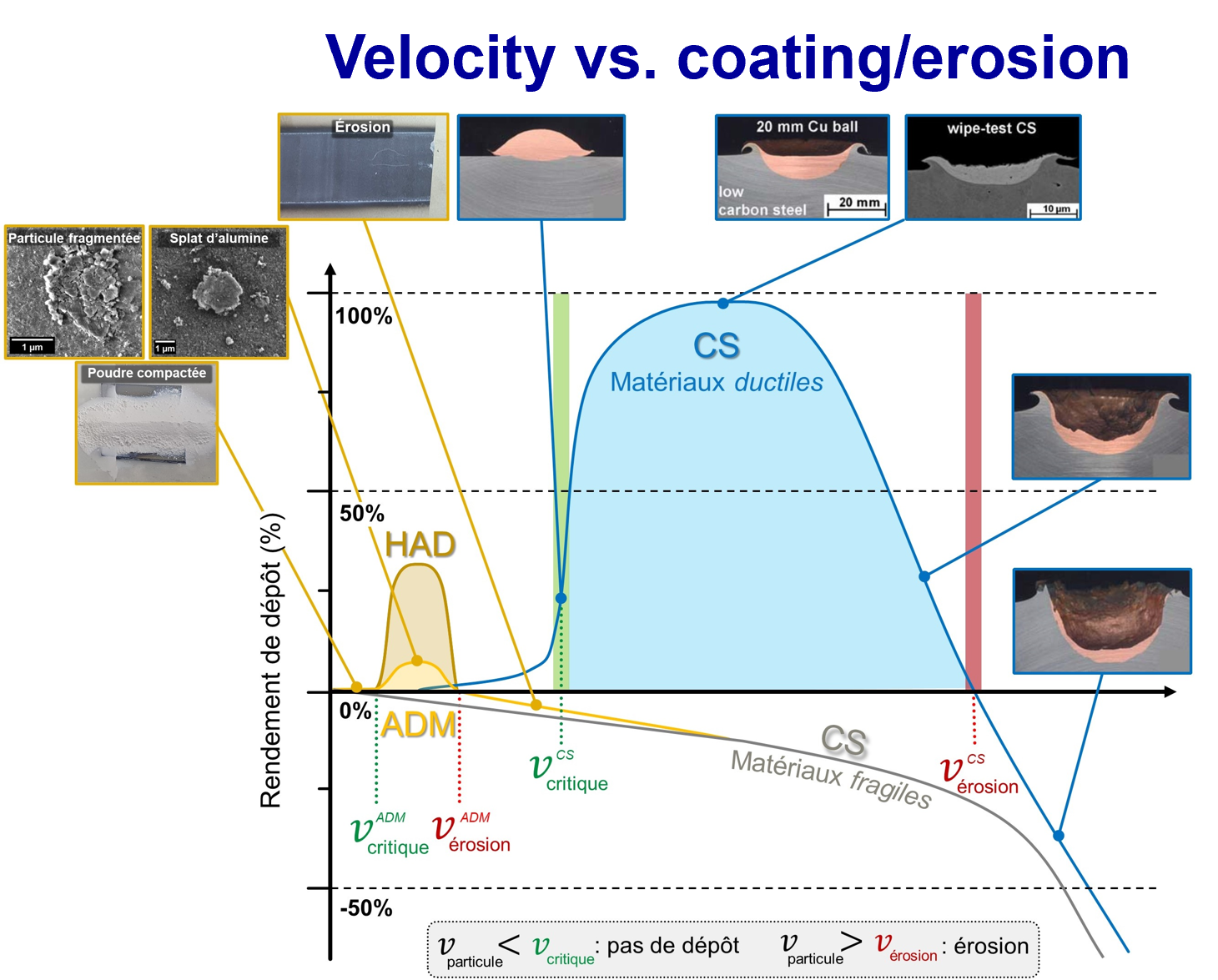
Référence bibliographique
D. Hanft, J. Exner, M. Schubert, T. Stöcker, P. Fuierer, R. Moos, An Overview of the Aerosol Deposition Method: Process Fundamentals and New Trends in Materials Applications, Journal of Ceramic Science and Technology 6 (2015) 147–182
Applications et innovation
L’ADM est une technologie polyvalente qui trouve des applications dans des domaines stratégiques variés, offrant des solutions innovantes pour l’industrie.
✔️ Électronique : dépôt de revêtements conducteurs et isolants. Fabrication de films minces pour dispositifs microélectroniques, y compris des matériaux piézoélectriques.
✔️ Énergie : production d’électrodes pour batteries lithium-ion et dispositifs de récupération d’énergie vibratoire. Applications possibles dans les supercondensateurs grâce à la possibilité de déposer des matériaux composites.
✔️ Médical : revêtements biocompatibles sur implants médicaux, offrant résistance à la corrosion et propriétés antibactériennes. Développement de surfaces fonctionnelles adaptées aux prothèses et dispositifs implantables.
✔️ Optique : fabrication de couches transparentes pour dispositifs optiques de précision. Revêtements protecteurs contre l’usure et les rayures pour lentilles et systèmes optiques avancés.
✔️ Aéronautique : dépôt de couches protectrices résistantes à l’usure, à la corrosion et aux variations thermiques pour composants critiques. Fabrication possible de barrières thermiques légères pour turbines et moteurs aéronautiques.
Défis et perspectives
Malgré les nombreux avantages offerts par l’ADM, certains défis subsistent, nécessitant des efforts continus de recherche et développement.
✔️ Contrôle des paramètres opératoires : la précision dans le contrôle des paramètres tels que la vitesse des particules, la pression du gaz et la distance de projection reste essentielle pour garantir la qualité des revêtements.
✔️ Adaptabilité des matériaux : étendre la gamme des matériaux compatibles avec l’ADM, en particulier pour les polymères et certains composites avancés, est une priorité pour les chercheurs. Cela inclut le développement de techniques spécifiques pour traiter des matériaux à faible densité ou thermosensibles.
✔️ Montée d’échelle : la mise à l’échelle industrielle du procédé ADM nécessite des investissements importants en infrastructure et en optimisation technologique. Les défis incluent la conception de systèmes capables de maintenir une homogénéité de dépôt sur de grandes surfaces ou des géométries complexes.
Cependant, ces défis sont contrebalancés par des caractéristiques qui positionnent l’ADM comme une technologie de pointe et une solution prometteuse pour l’avenir. Sa capacité à produire des revêtements céramiques denses à température ambiante, combinée à une consommation énergétique réduite et une flexibilité sur la nature des substrats traités, en fait une méthode respectueuse de l’environnement et parfaitement alignée avec les exigences croissantes de durabilité industrielle. De plus, les avancées récentes dans l’optimisation des poudres, l’intégration de matériaux composites et l’amélioration des cinétiques de dépôt ouvrent la voie à de nouvelles applications.
Avec son potentiel d’adaptation et d’innovation, l’ADM représente bien plus qu’une méthode de dépôt : c’est une technologie stratégique pour développer des matériaux avancés à faible impact environnemental, répondant aux besoins actuels et futurs des industries les plus exigeantes.