CERAGREEN 3D
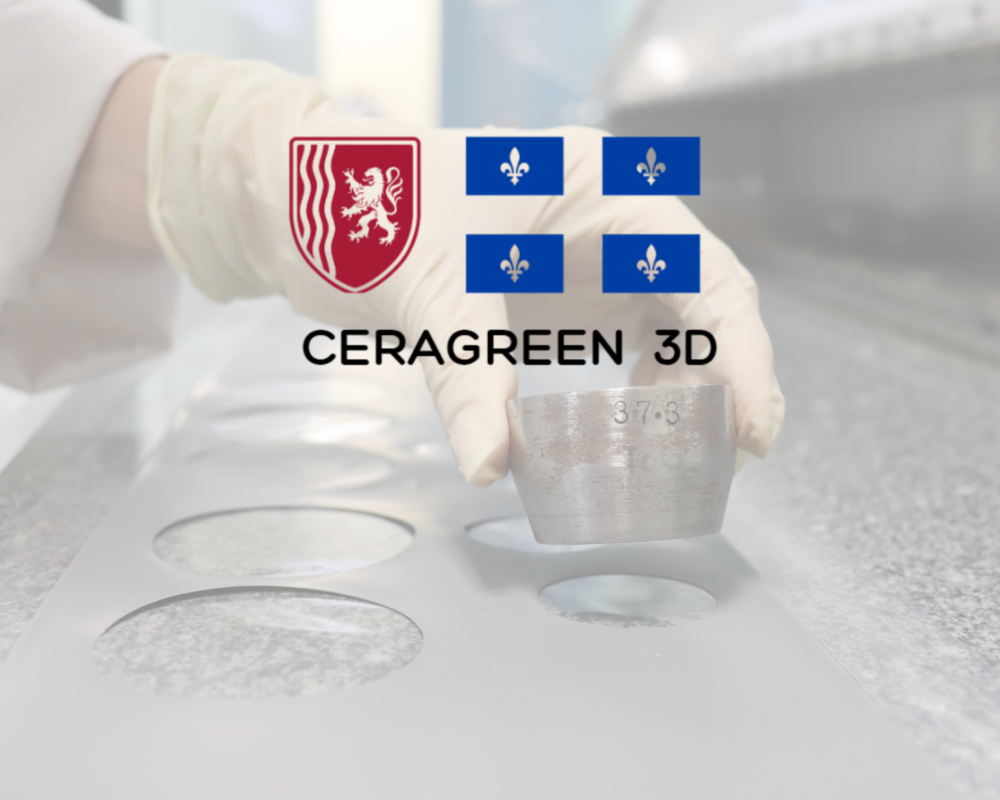
13 Nov 24
Articles
Temps de lecture : 5 minutes
Le projet CERAGREEN 3D représente un des axes du volet ADDICERAM partie intégrante de notre programme de ressourcement CERA 3+.
Le volet ADDICERAM a pour objectif le développement de technologies de fabrication additive des céramiques et multi-matériaux. Le procédé de projection de liant sur lit de poudre (projet CERAJETTING)est concerné. Les procédés de stéréolithographie et de microdispensing pour la réalisation de composants optiques (projet OPTICERAM)sont concernés. L’impression 3D de feedstocks céramiques éco-responsables (projet CERAGREEN 3D)sont également concernés.
Dans le cadre du projet CERAGREEN 3D, le CTTC collabore avec des partenaires canadiens (COALIA, Université de Sherbrooke, FabLab Inc) pour développer des feedstocks biosourcés adaptés à la fabrication de pièces céramiques de formes complexes par impression 3D. L’enjeu principal est de réduire l’impact environnemental que les auxiliaires organiques pétrosourcés, utilisés pour la formulation, ainsi que les traitements thermiques appliqués après la mise en forme (notamment le déliantage). Ce projet a démarré en juin 2023 et se déroulera jusqu’en juin 2026.
Du choix des matières premières et de la mise en forme…
Le déroulement du projet CERAGREEN 3D passe dans un premier temps par la sélection de matières biosourcées. Puis part des essais de préparations de feedstocks à l’échelle laboratoire. Des essais préliminaires de mélange en bain de sable permettent d’observer le comportement des différents additifs avec la poudre céramique. La caractérisation du comportement rhéologique des feedstocks biosourcés vient en complément afin de les comparer à des matières commerciales servant de référence. La masse de poudre maximale incorporée permet alors de déterminer un taux de charge qu'il convient de maximiser, en accord avec le procédé de mise en forme visé.
Dans le cadre du projet CERAGREEN 3D, l'équipe utilise le procédé de mise en forme micro-extrusion pilotée (ou Robocasting) à partir de granules (procédé FGF : Fused Granular Fabrication) ou de filament le cas échéant(procédé FFF : Fused Filament Fabrication).
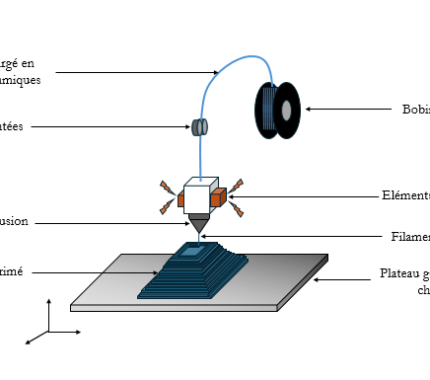
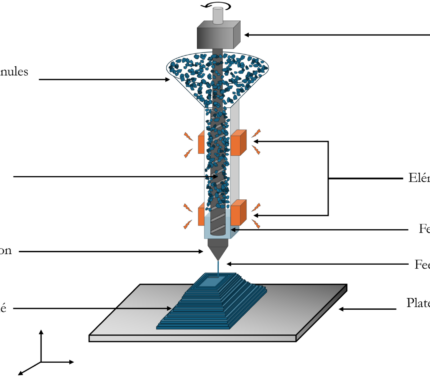
Figure 1. Schémas des procédés FFF (a) et FGF (b)
Une fois la formulation du feedstock validée d’un point de vue rhéologique et de taux de charge, une préparation en plus grande quantité est réalisée dans des malaxeurs appropriés. Les feedstocks sont ensuite concassés et tamisés ou directement extrudés au travers d’une filière équipée d’un couteau rotatif afin d’obtenir des granules calibrés.
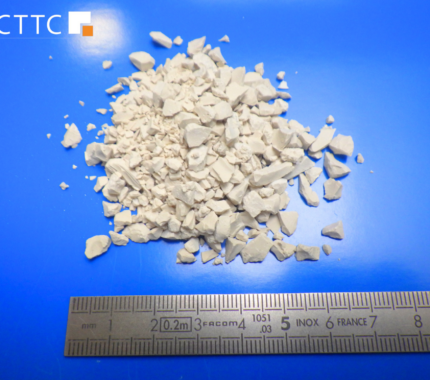
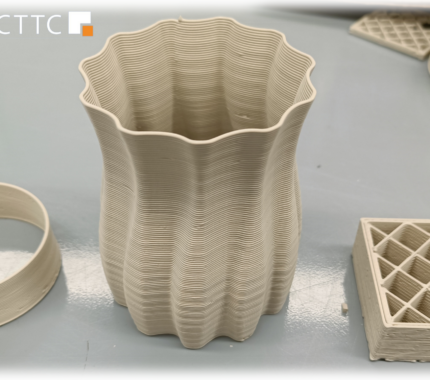
Figure 2. Photographies de granules calibrés (à gauche) et exemples de pièces « vertes » de géométries différentes imprimées par FGF à partir d’un feedstock biosourcé
… à l’obtention de pièces finales écoresponsables.
Une fois les pièces mises en forme, une étape de déliantage est appliquée. Contrairement à ce qui est couramment réalisé pour les pièces céramiques (injectées par exemple) afin d’éliminer les additifs organiques utilisés via un déliantage thermique, le consortium CERAGREEN 3D ambitionne le recours à un déliantage par extraction des organiques au moyen de CO2 supercritique (CO2 SC).
Dans des conditions appropriées de température et de pression, le CO2 passe en effet à l’état supercritique et présente des caractéristiques (de viscosité notamment) permettant l’extraction/la solubilisation partielle voire totale de certaines matières organiques.
![Figure 3. Diagramme de phase du CO2 [Radwan Chahal. Capteurs optiques en fibres de verre de chalcogénure dopées terres rares appliqués à la surveillance du stockage géologique de CO2. Matériaux. Université de Rennes 1, 2015. Francais.]](https://www.cttc.fr/wp-content/uploads/2024/11/diagramme-de-phase-du-co2.png)
En plus de permettre la récupération des additifs extraits, les autres avantages de ce type de déliantage sont la durée de traitement, généralement plus courte par rapport au déliantage thermique, ainsi que la réduction des émissions de gaz à effet de serre du fait de l’absence de combustion des organiques par oxydation en température. Le CO2 SC représente également une alternative à certains autres solvants organiques utilisés (éthanol, acétone, hexane) ou au déliantage catalytique.
Une fois déliantées dans des conditions optimisées, les pièces sont frittées et contrôlées par différentes techniques de mesure. La morphologie macroscopique et microscopique est analysée principalement par microscopie numérique et microscopie électronique à balayage, permettant également de vérifier l’absence de défauts tels que des microfissures. La densité est déterminée par pesée hydrostatique afin de déterminer la porosité des échantillons. Le projet CERAGREEN 3D s’inscrivant dans un cadre éco-responsable, des méthodes de caractérisations non destructives (CND) sont également exploitées afin de remonter à certaines propriétés.
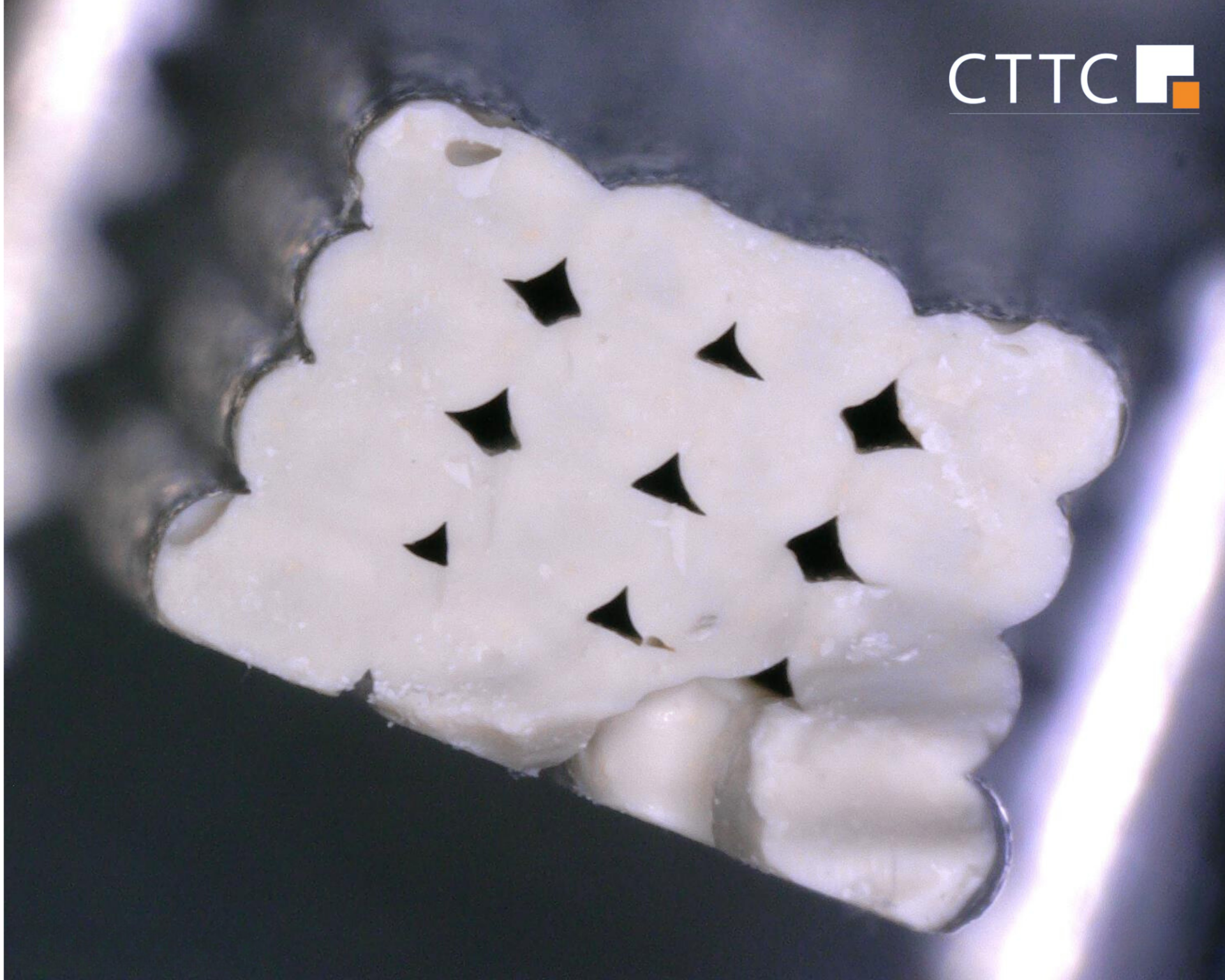
Le projet à l’heure actuelle
A ce jour, les efforts consentis dans le cadre du projet CERAGREEN 3D ont permis de développer en particulier un feedstock céramique à base d’alumine, imprimable à partir de granules dont le système de liants est constitué exclusivement de matières biosourcées. Ce feedstock présente un taux de charge satisfaisant mais son optimisation est toujours en cours, en travaillant notamment sur sa composition.
L’optimisation des paramètres d’impressions est également en cours afin d’augmenter la résolution et d’obtenir un état de surface des pièces amélioré. En ce qui concerne les post-traitements des pièces imprimées, des essais de déliantage en CO2 SC sont à l’étude à l’aide d’échantillons tests. Ces essais vont permettre de déterminer les paramètres optimaux permettant d’éliminer et de récupérer un maximum d’auxiliaires organiques biosourcés. Une attention particulière sera portée à la fois sur la conservation de la géométrie initiale des pièces imprimées ainsi que sur leur tenue mécanique avant traitement thermique de frittage. Ce traitement thermique est également en cours d’optimisation afin d’atteindre une densification des pièces la plus élevée possible sans que celles-ci ne présentent de défauts microstructuraux.
En fonction de l’ensemble des résultats issus des diverses améliorations matériaux et procédés décrites ci-dessus, le développement d’autres feedstocks sera envisagé ainsi que l’incorporation d’autres types de poudres céramiques afin de diversifier le portfolio matériau.
Remerciement et Partenariats
Le CTTC tient à remercier l’Union Européenne ainsi que la Région Nouvelle-Aquitaine pour leur confiance et leur soutien financier. Sans cet accompagnement, un projet de cette envergure serait difficile à mener.
Le CTTC remercie également les différents partenaires qui participe aux différents projets de ce programme.
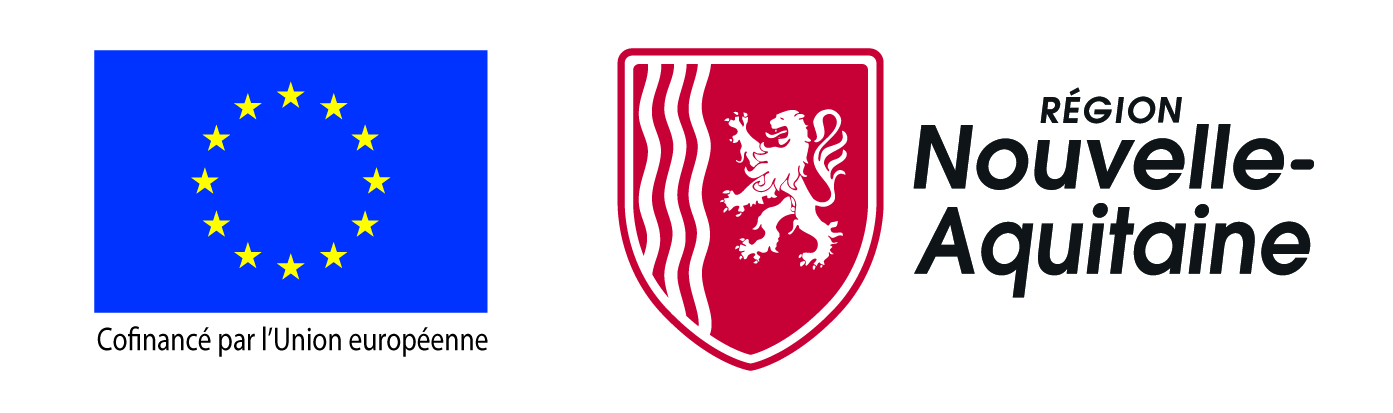