Oxide technical ceramics
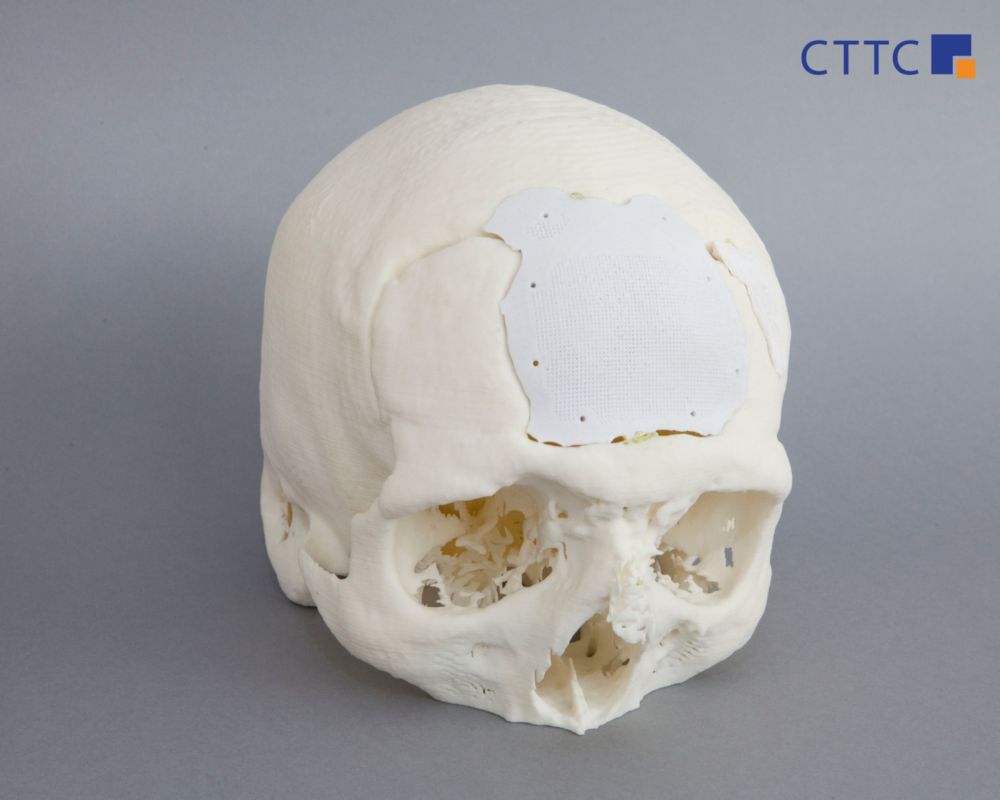
08 Nov 24
Articles
Our series on technical ceramics continues. This week we invite you to discover an article dedicated to oxide ceramics.
What are oxide technical ceramics?
In so-called technical industrial ceramics, we can distinguish between oxides and non-oxides. The latter will be the subject of a later article.
Oxide ceramics are inorganic chemical compounds formed by the association of a metal and one or more oxygen atoms, linked together by iono-covalent bonds. They are mainly extracted from mines and purified chemically. Alumina, the ceramic material most widely used in industrial applications, is - initially - one of the most abundant constituents of the earth's crust. It is second only to silica, which alone accounts for 50% by mass of the rocks on the Earth's surface, with alumina making up 25%.
These oxide materials can also be obtained by chemical synthesis, particularly when high purities (greater than 99%) are required.
To obtain the desired characteristics of the ceramic material, it is important to control all the stages of the process used (detailed in this article) and this starts with controlling the characteristics of the powder (grain size and shape, purity, nature of the surface, density, etc.).
After shaping, these oxide materials are densified by heat treatment in air, whereas non-oxides require specific atmospheres.
Oxide ceramics have remarkable properties, including resistance to high temperatures, high mechanical strength, chemical inertness, high hardness, low density and excellent electrical insulation. They are also characterised by their high resistance to abrasion and friction, low thermal conductivity and dimensional stability at temperature.
A few examples:
- Alumina (Al2O3)
- Silica (SiO2)
- Zirconia (ZrO2)
- Rutile (TiO2)
- Cordierite (2MgO,2Al2O3,5SiO2)
- Mullite (3Al2O3, 2SiO2)
- Magnesia (MgO)
- Uranium oxide (UO2)
Which industries use oxide ceramics?
In general, oxide ceramics can be found in many fields of application because of their special properties, such as :
Electronics & Telecommunications: high dielectric constant and low losses, ideal for applications such as antennas, resonators, filters, etc.
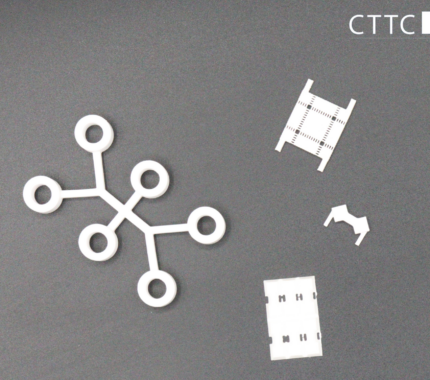
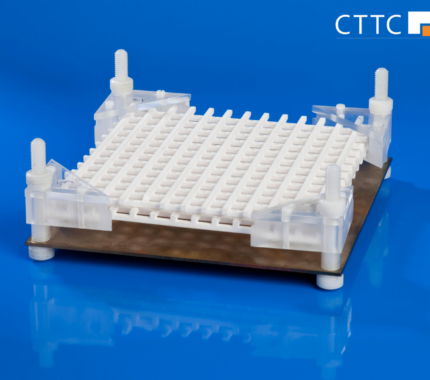
Aerospace: low density, high temperature resistance and electrical insulation for applications such as insulators, radomes, connectors, ....
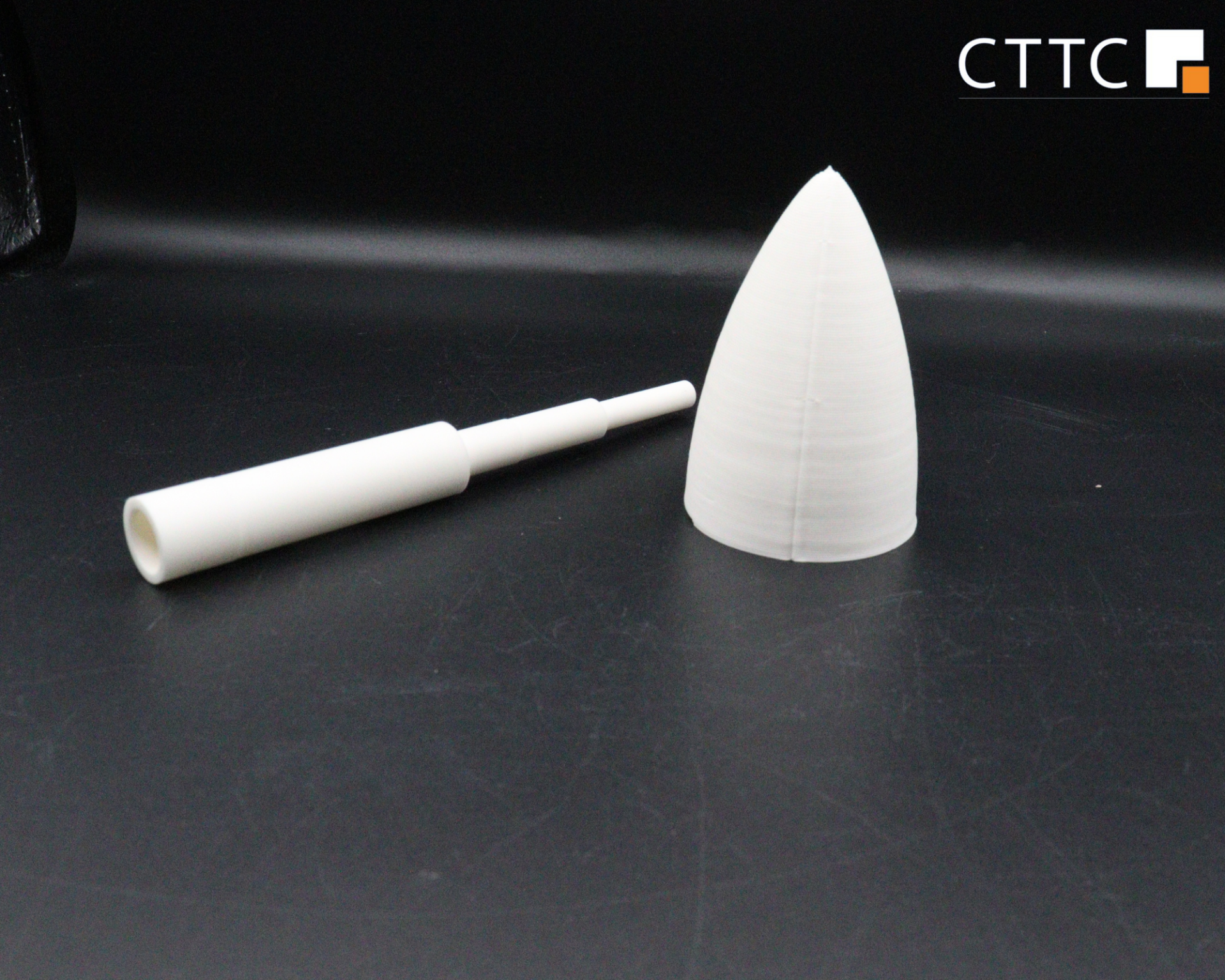
Medical: chemical inertness, wear resistance, mechanical strength, for applications such as implants, prostheses, bone fillers, ....
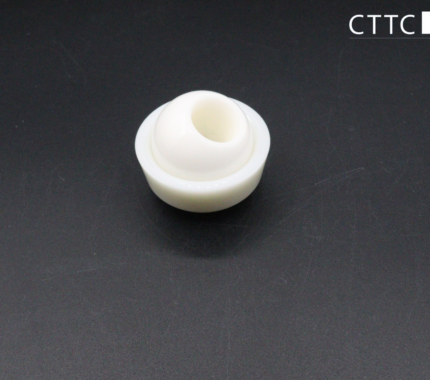
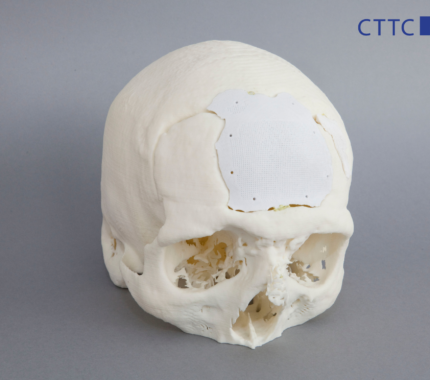
Automotive: temperature stability, thermal shock resistance, ionic conduction for applications such as catalyst supports, particle filters and lambda sensors.
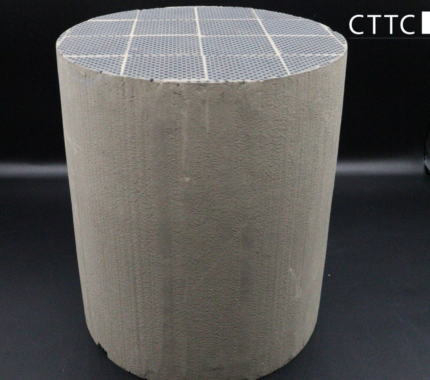
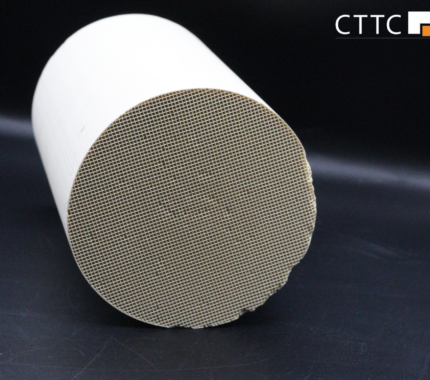
The advantages
Thanks to their intrinsic properties, oxide ceramics meet a wide range of industrial requirements, where polymers and metals - and even superalloys - reach their limits.
Heat treatment does not require any special equipment, as the materials are densified in air.
The disadvantages
Whatever the process used to shape an oxide ceramic part, control of each stage means that very strict dimensional tolerances (less than +/- 0.05mm) cannot be met. Ultrasonic machining or, more conventionally, grinding is therefore always necessary. Given the high hardness of oxides, diamond tools must be used.
The cost
As mentioned above, machining is an essential final stage in the production of a ceramic part to the required dimensions. This stage requires costly special tools, and can take a long time to complete.
The search for tight tolerances can therefore result in significant additional costs.
Conclusion
In conclusion, thanks to their exceptional properties, technical oxide ceramics play a major role in many industrial sectors. Their mechanical strength, refractoriness, low thermal expansion and chemical inertness make them key materials for a wide range of applications, from electronics and aerospace to the medical and automotive sectors. However, achieving these properties means mastering every stage of the forming process used. What's more, meeting tight dimensional requirements involves a final machining phase, which may explain the high cost of the parts.
Despite these challenges, oxide ceramics remain unavoidable solutions to the limitations of traditional materials.
As a technical centre, the CTTC plays a central role in the research and development of these materials.