Non-oxide technical ceramics
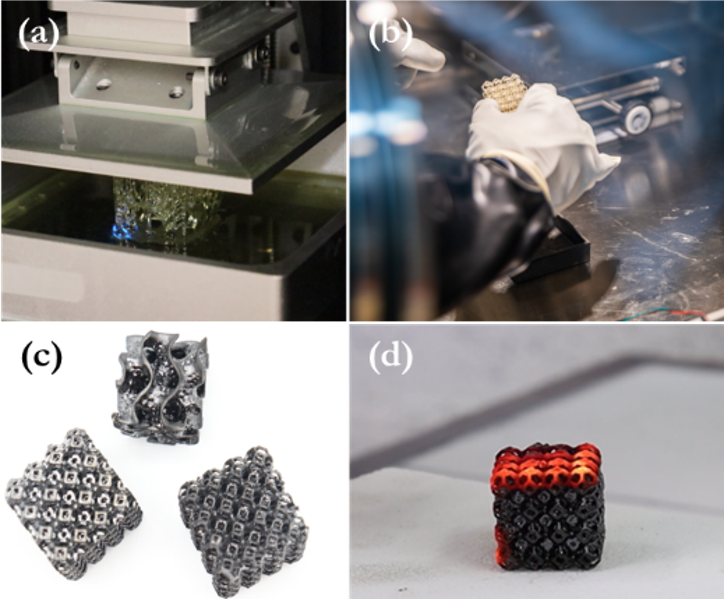
05 Dec 24
Articles
We're continuing our series on technical ceramics. After Technical Ceramics: Properties and Applications in Industry, and Oxide Technical Ceramics, this week we present an article dedicated to non-oxide technical ceramics.
What are non-oxide technical ceramics?
Non-oxide technical ceramics
Technical ceramics are defined as “non-oxide” by their chemical composition. Indeed, as their name suggests, they do not incorporate oxygen, but other elements. These include boron, carbon or nitrogen, leading to categories known as borides, carbides or nitrides (see table below). In general, non-oxide technical ceramics have higher properties than oxide ceramics. However, they do have their limitations, particularly in oxidizing atmospheres.
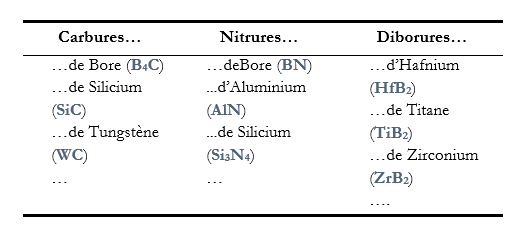
Other types of non-oxide ceramics
Other types of non-oxide ceramics offer unique properties, such as phosphides or mixed carbides and nitrides. These materials (including MAX phases: Ti3SiC2, Ti2AlC, …)will be the subject of a future article.
Like oxide ceramics, non-oxide ceramics can be synthesized thermally, mechanically or chemically. They are available in the form of objects or coatings.
Carbide powders are generally obtained by a high-temperature reaction (1600-2500°C) between a carbon source (coke) and the associated metal oxide (SiO2 for SiC, etc.). This reaction takes place under specific conditions (neutral or reactive atmosphere, reduced pressure, under hydrogen, etc.).
These oxide precursors can be heat-treated in a nitrogen atmosphere to convert them into nitrides.
The synthesis of borides (with ultrarefractory properties) is far more specific, requiring silicothermal, magnesothermal or carboborothermal reactions.
Certain compounds, such as boron phosphide (B12P2), can be produced from suitable precursors by mechanosynthesis.
In particular, these materials are being developed by CTTC as part of the CAPBAB project (ANR ASTRID) in collaboration with the IMPMC, LSPM, 3SR and IRCER laboratories. CTTC has focused on scaling up powder synthesis and sintering large samples.
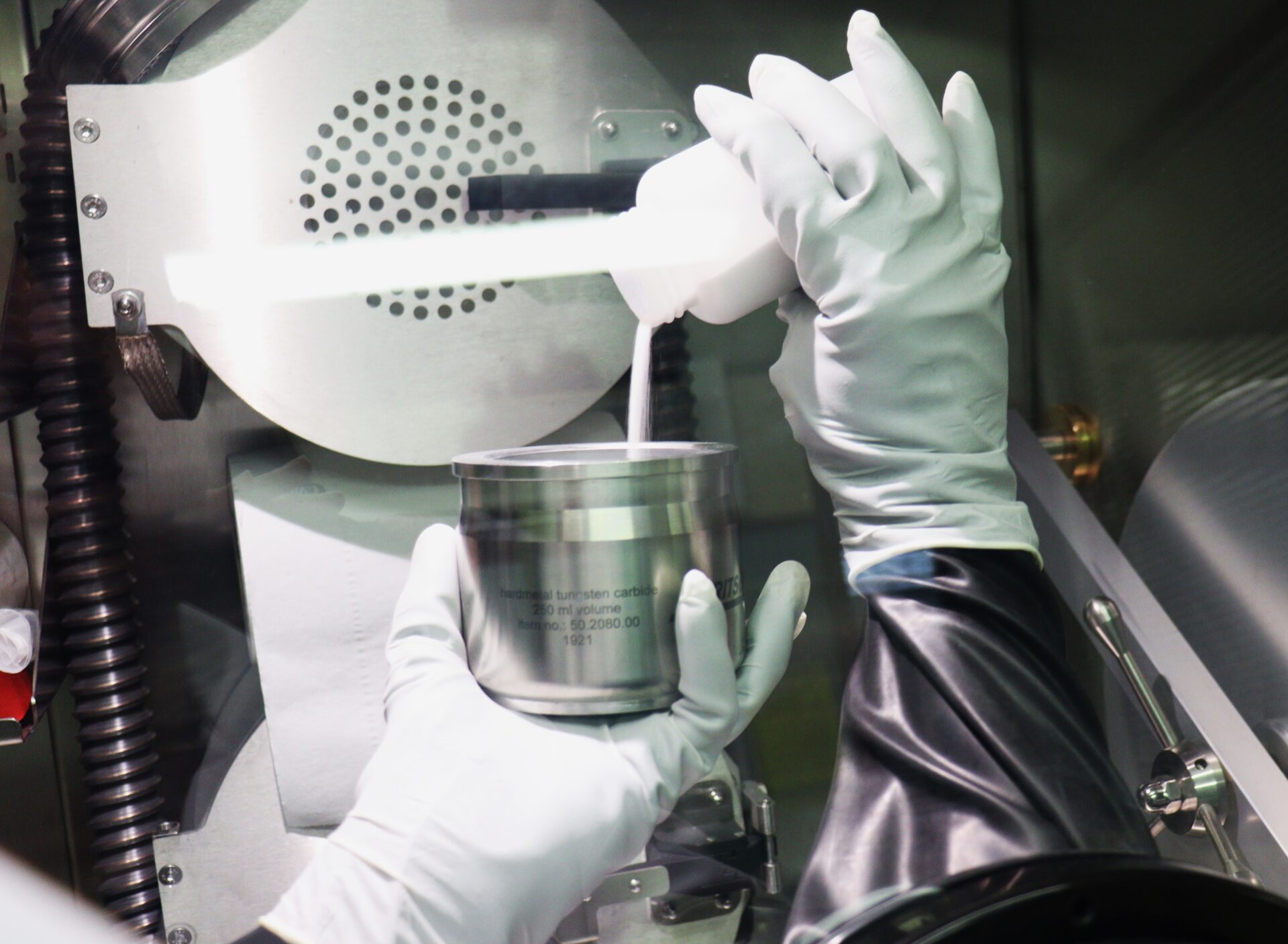
These materials, which lack oxygen in their crystalline structure, require specific equipment and operating conditions. These requirements include a suitable temperature and a controlled atmosphere, which are far more stringent than air treatment.
Sintering under stress (pressure, atmosphere, electrical energy) often plays an indispensable role in densifying the material. Natural sintering of these ceramics can be envisaged, but requires the application of temperatures often in excess of 2200°C in a controlled atmosphere.
CTTC has implemented flash sintering (or SPS, Spark Plasma Sintering), a well-known technology for the production of dense ceramics. A schematic diagram is shown in Figure 2.
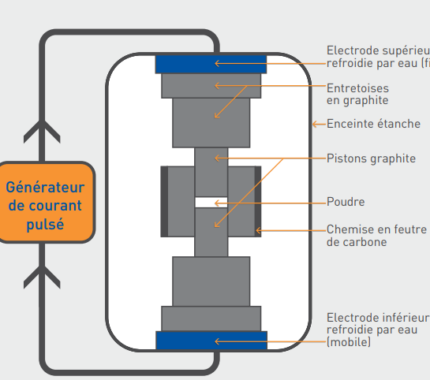
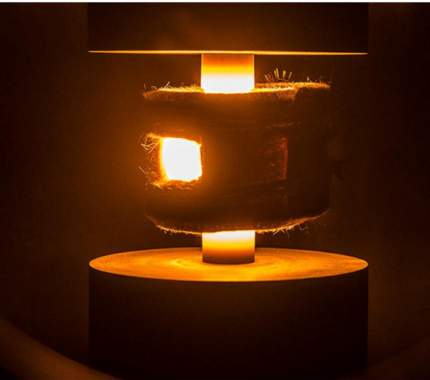
Figure 2. Material shaping by flash sintering by Claude ESTOURNES[1]
[1] Adapted from the reference “Mise en forme de matériaux par frittage flash”, Techniques de l'ingénieur, In56, 2006
This technique makes it possible to obtain very fine microstructures after sintering, while retaining the initial powder grain size. It also enables very high mechanical performances to be achieved.
Abrasives, cutting tools, drilling, grinding and ballistic protection
Silicon carbide (SiC), boron carbide (B4C), tungsten carbide (WC), cubic boron nitride (c-BN) and titanium diboride (TiB2) are very hard ceramics. These hardnesses (28, 31, 25, 46 and 30GPa) enable them to be used as abrasives, cutting, drilling or grinding tools.
These hardnesses and low densities (2.5 g.cm-3) enable carbides to be used as ballistic protection. For example, B4C and 31GPa are used in this field (Figure 3).
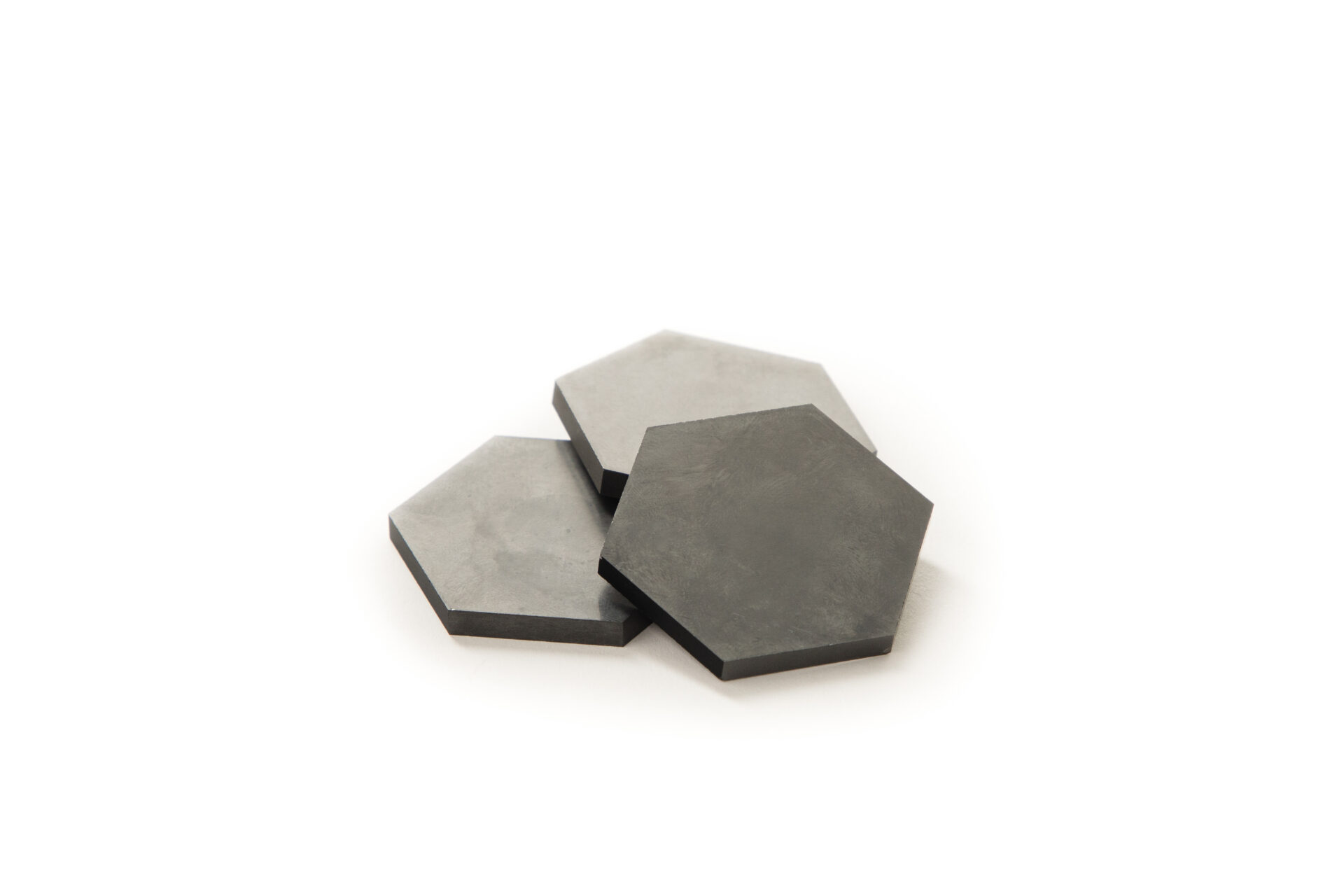
Separation and treatment of gaseous and liquid effluents
Silicon carbide (SiC) combines chemical and thermal stability with ease of shaping for porous devices. Figure 4).
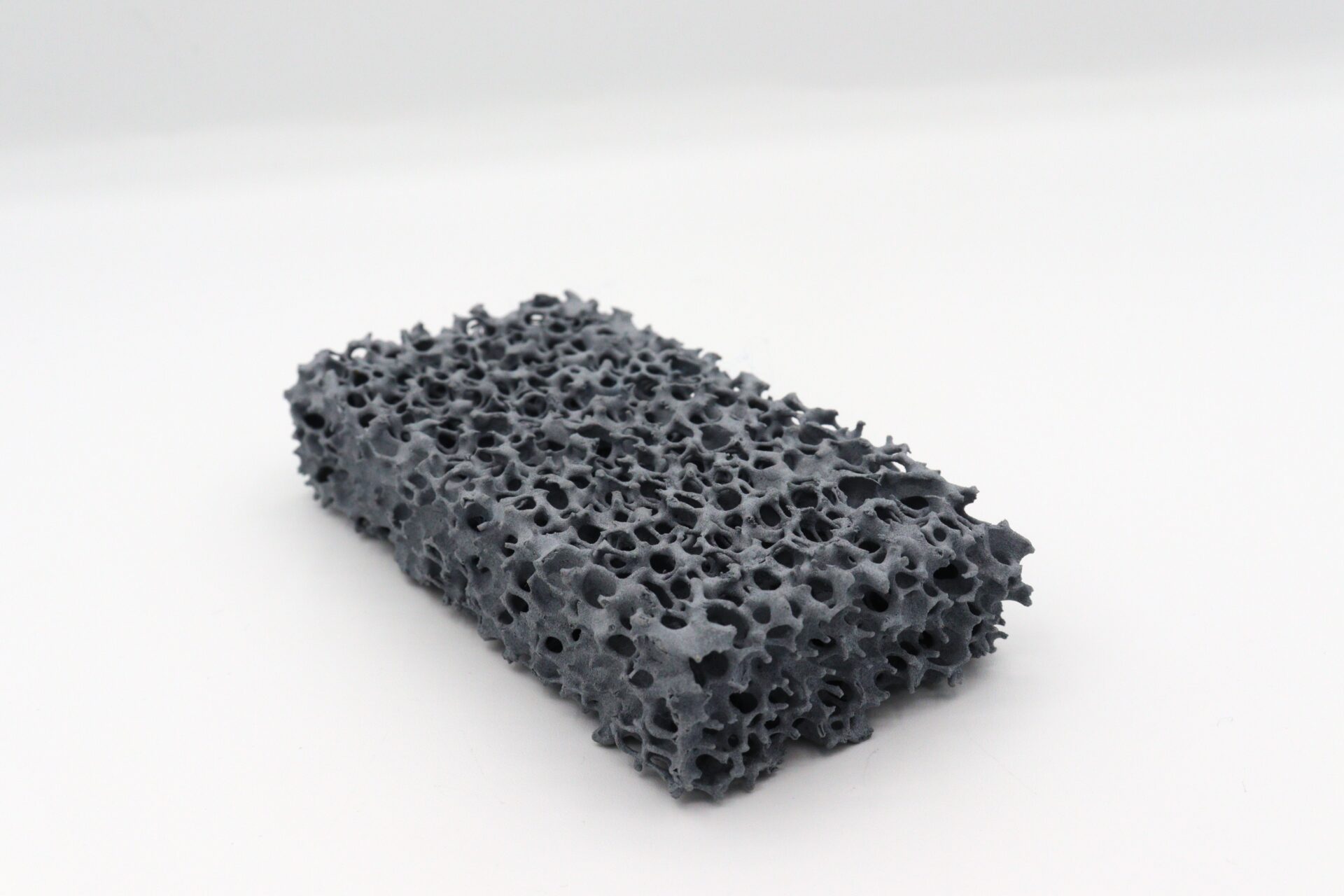
Automotive, aeronautics and space
Hexagonal boron nitride (h-BN), similar to graphite, serves as a solid lubricant under reduced-pressure conditions.
Silicon nitride (Si3N4), resistant to abrasion and friction, is mainly used in ceramic ball bearings. It is used in the automotive and transportation industries.
Silicon carbide (SiC) is used as a mirror for space applications.
Electronics and telecommunications
Aluminum nitride (AlN) is used in optoelectronics, power electronics and dielectric substrates or deposits.
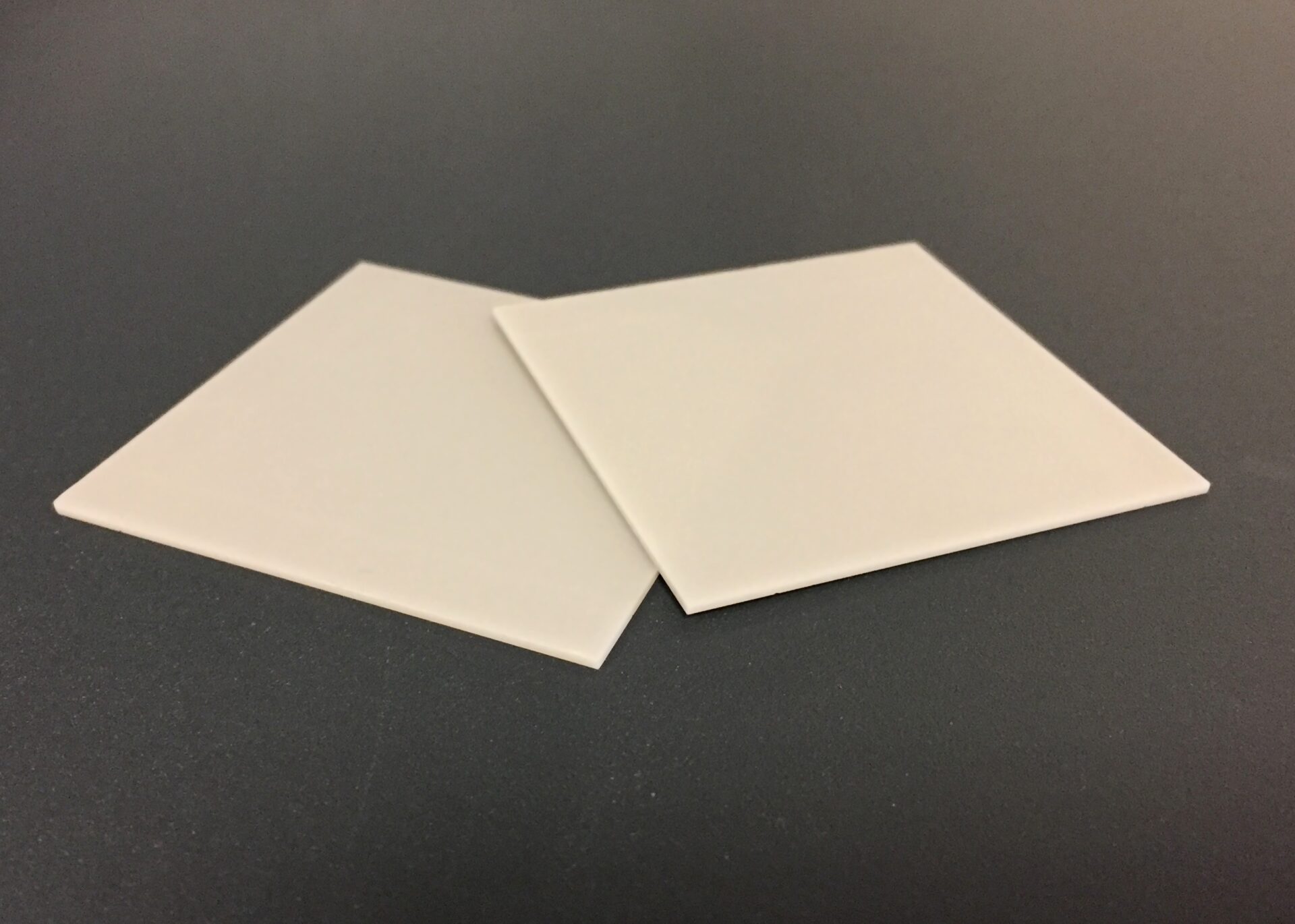
Its high thermal conductivity for a ceramic (approx. 200W.m-1.K-1) means that it is more efficient at dissipating heat than alumina or zirconia. SiC is also used in LED systems, as it can be a broadband semiconductor.
Ultrarefractory
Non-oxide materials, mainly diborides and carbides (HfC, HfB2, TiB2, ZrB2, …) are stable up to temperatures in excess of 2000°C. This outstanding feature makes it possible to solve nuclear fuel conditioning problems.
Disadvantages of non-oxide technical ceramics
Non-oxide, shaped objects have limited dimensional tolerances. Beyond +/-0.15mm, (“Near Net Sape”), a grinding step by machining is indispensable. This grinding is more demanding for non-oxide ceramics, due to their higher hardness than machining tools (carbides, diamond).
Densification (sintering) in air is impossible due to oxidation.) It is carried out in specific atmospheres.
These two main constraints call for the acquisition and mastery of complex and costly equipment, both in terms of purchase and operating time.
The advantages of non-oxide technical ceramics
The specific properties of non-oxides mean that they can meet many industrial requirements where other materials reach their limits.
Despite their drawbacks, non-oxide ceramics are indispensable when operating conditions are extreme.
The last word
The industry, in its constant quest for performance, is working hard to develop incremental and breakthrough innovations. The industry is increasingly interested in the shaping of complex geometries, thanks to Additive Manufacturing of ceramics, and flash sintering of shaped parts.
Among the so-called “Near Net Shape” processes, Binder-Jetting (Figure 6) is used to produce complex SiC parts.
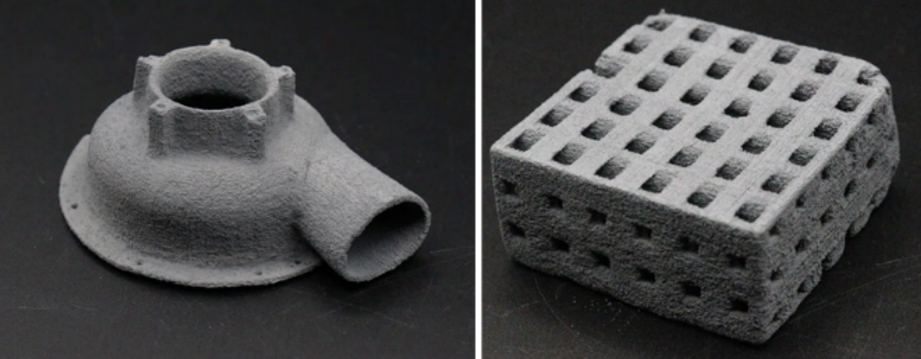
Another approach is to use stereolithography (SLA), with a photoreactive raw material. A ceramization heat treatment produces a silicon oxycarbide (the so-called preceramic polymer route). CTTC, in collaboration with one of its partners, has recently developed this approach.
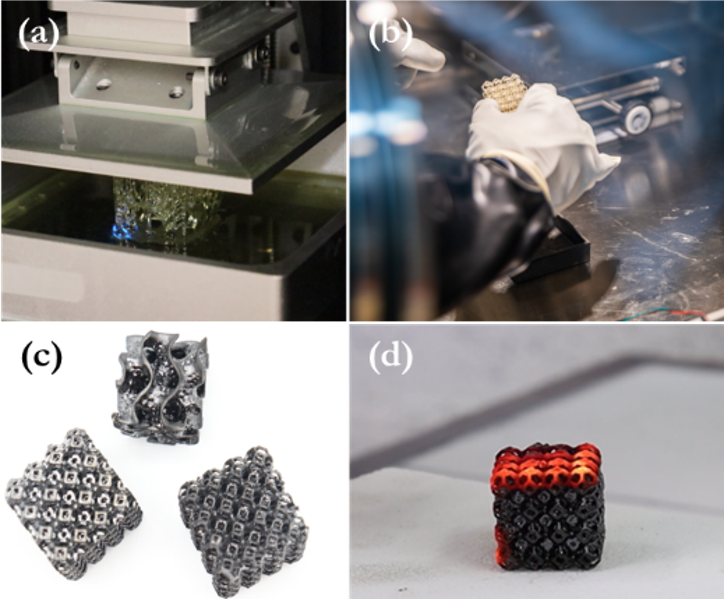
Thanks to their exceptional properties, non-oxide ceramics play a major role in many industrial sectors. However, they remain confidential (apart from silicon carbide).
Their high hardness, chemical, mechanical and thermal resistance make them key players in many industrial sectors. They are used in the automotive, space, defense, filtration, grinding and cutting industries. Obtaining objects with perfectly controlled properties is no easy task. Each stage of the process requires perfect mastery. As a technical center, the CTTC plays a central role in the research and development of these materials.