Traditional ceramics for technical applications
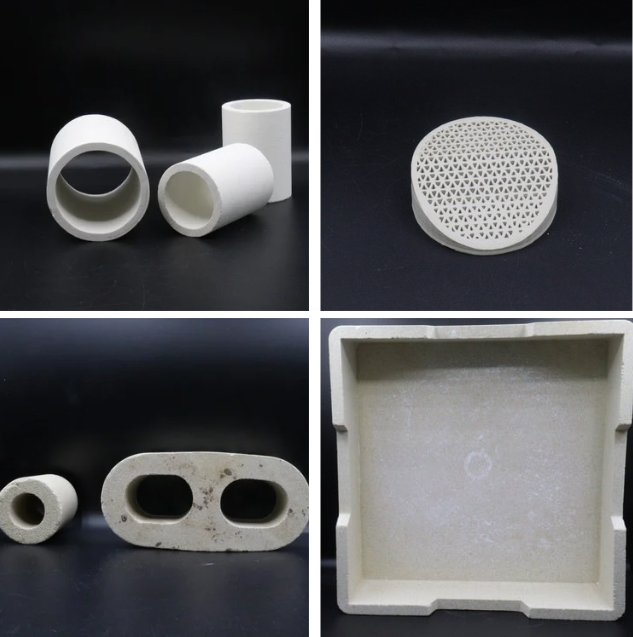
13 Feb 25
Articles
Reading time: 5 minutes
Our series on technical ceramics continues. This week, we offer you an article dedicated to traditional ceramics for technical applications.
Traditional ceramics
Traditional ceramics have accompanied us for millennia. Made from natural materials such as clays, feldspars, and silicate minerals, they are formed through a high-temperature firing process, granting them strength, durability, and a unique aesthetic.
Traditional ceramics can be classified into several categories, such as terracotta, earthenware, stoneware, and porcelain, each possessing its own characteristics.
Depending on the geometry and characteristics of the pieces to be produced, traditional ceramics can be shaped by various methods: natural casting or under pressure from an aqueous suspension in a porous mold, extrusion, calibration, injection of a plastic paste, or pressing granules.
In addition to their aesthetic appeal, these ceramics exhibit exceptional properties, including excellent thermal resistance, high electrical insulation, and very low chemical reactivity. These advantages make them essential materials for numerous everyday applications as well as in industries such as electronics, energy, and the environment.
Thus, the first developments in the field of technical ceramics began with the use of silicate ceramics, such as technical porcelains, steatite, mullite, and cordierite.
Traditional ceramics for technical applications
Technical porcelains
Porcelain is primarily used in tableware, but its electrical insulating properties have led to the production of insulating components in the electrical industry (such as switches and insulators). As a result, a specialized variation of this material exists: technical porcelains.
These are alumina-based porcelains, made from a paste enriched with Al₂O₃ (corundum or calcined alumina) at a concentration exceeding 50%. In this case, clays are used for their plasticity properties, making the powder mixture suitable for shaping. The products are generally sintered (and sometimes glazed) at temperatures ranging from 1280 to 1600°C, depending on the alumina content.
One application example is power resistors, which absorb current surges and dissipate them as heat. The material consists of an insulating ceramic matrix (based on clay and alumina) combined with a conductive metallic phase.
Steatite
Steatite is a mineral talc with the chemical formula (3MgO·4SiO₂·H₂O), which may also contain other minerals such as chlorite, magnesite, dolomite, and sometimes small amounts of quartz.
Used since antiquity, steatite was employed by civilizations such as the Egyptians and Mesopotamians to craft decorative objects, sculptures, and ritual tools. Today, it is widely used in various fields, including the manufacturing of kitchen countertops, sinks, and fireplaces.
Thanks to its ability to store and gradually release heat, steatite has been extensively used in the production of natural heating systems (radiators). This process relies on the principle of dry inertia, in which heat is accumulated within a steatite heating core and later emitted as radiant energy.
Additionally, steatite is used in the refractory coatings industry and for electrical insulation due to its thermal stability and dielectric properties.
Mullite
Mullite is a stoichiometric compound of alumina and silica with the chemical formula 3Al₂SiO₅.
Although mullite is a natural mineral, its deposits are extremely rare. Industrial applications rely on synthetic mullites, which are produced through high-temperature calcination of various natural or processed alumino-silicates. Among these materials, kaolin and certain refractory clays such as andalusite are commonly used.
Another method involves stoichiometrically mixing fine powders of alumina and silica, which transform into mullite through high-temperature sintering. Several parameters play a fundamental role in mullite formation and the development of its final properties. Among these, the choice of raw materials is particularly important to ensure the quality of the final product. Other key factors include grain size, mixture homogeneity, synthesis temperature, firing duration, and atmospheric conditions during processing.
This material exhibits remarkable refractory properties, notably a high melting point of 1853°C, ensuring its thermal stability. It also offers good resistance to high temperatures (up to 1400°C), making it suitable for use in extreme environments.
Mullite also offers excellent thermal shock resistance and low thermal expansion, ensuring great stability. This provides it with high dimensional stability, even at elevated temperatures.
Its low thermal conductivity makes it suitable for use as a thermal insulator.
Mullite is therefore particularly used in the manufacturing of heating element supports, electric resistance supports, furnace refractories, melting crucibles, and more.
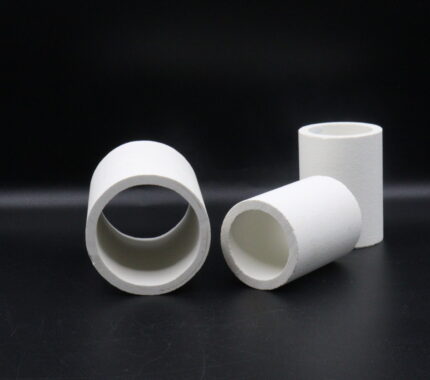
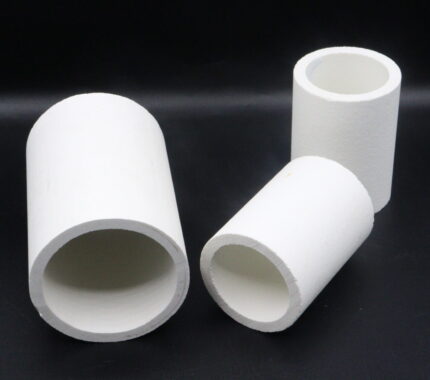
Cordierite
Cordierite is a magnesium aluminosilicate with the chemical formula 2MgO·2Al₂O₃·5SiO₂, typically derived from sedimentary rocks but can also be synthesized through various processes. It exhibits excellent thermal shock resistance due to its low coefficient of thermal expansion and low thermal conductivity.
Cordierite also offers good performance at high temperatures, with low dielectric losses, making it suitable for various applications. Additionally, it has outstanding resistance to corrosion, particularly against molten metals.
The applications are diverse: electrical insulation for heating elements, cooking supports, burners, catalytic converters for the conversion of pollutants such as CO, HC, and NOx, and supports for electronic components in the aerospace industry.
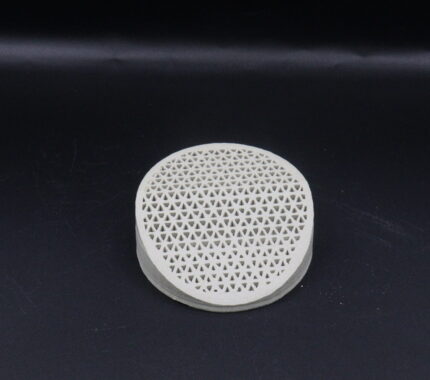
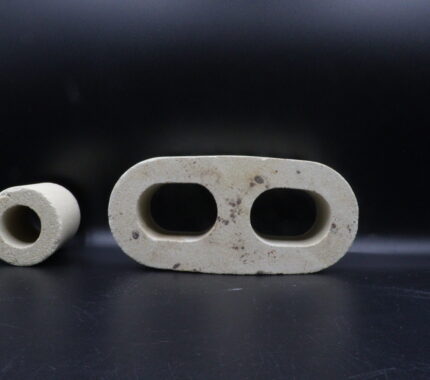
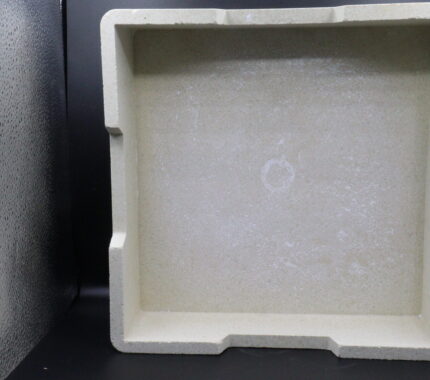
Contact us
The CTTC, as a technical center, we play a central role in research and development on these materials.
For more information, contact us: contact@cttc.fr