Aerosol Deposition Method –ADM
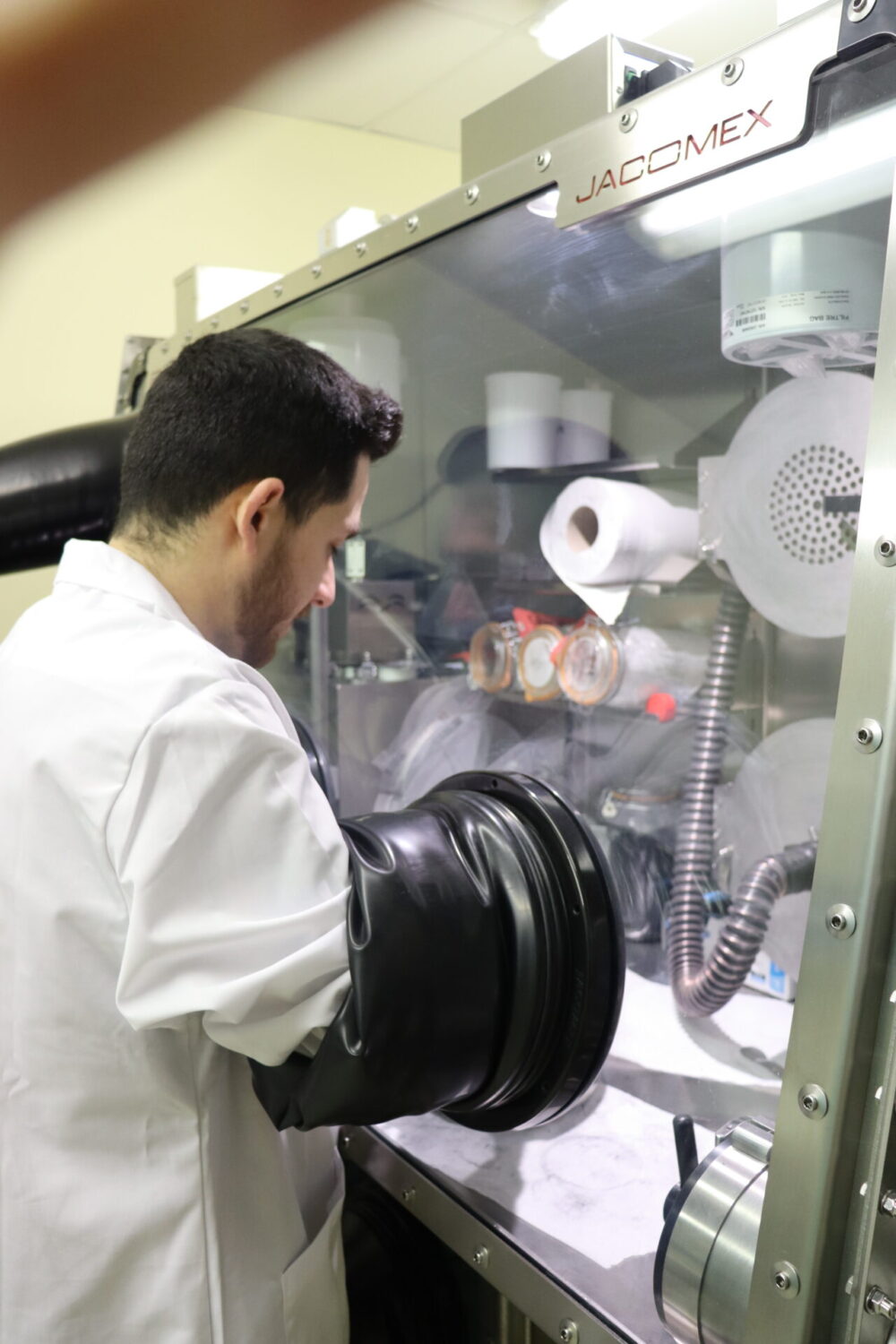
26 Feb 25
Articles
Reading time: 16 minutes
Aerosol Deposition Method (ADM), an innovative technology for ceramic coatings with low environmental impact
Our series of articles on ADM continues. After an article on ADM in general, this week we offer you an insight into the advantages of such a method.
The Aerosol Deposition Method (ADM) is an innovative technique for forming ceramic coatings (and sometimes metallic ones) at room temperature. This technology is primarily characterized by the formation of dense (> 95%), nanostructured coatings with micrometer thickness [1].
ADM was developed in the 1990s in Japan. The formation of coatings primarily exploits the plasticity of ceramic particles at the submicrometric/nanometric scale. This phenomenon is also observed in metals in the form of amplified localized deformation. To achieve this, fine dry particles (submicrometric to a few micrometers) are accelerated at speeds between 100–600 m/s until they impact a substrate. The kinetic energy of these particles promotes their deformation, fragmentation, and the formation of highly reactive surfaces, leading to the consolidation and densification of layers on a substrate without the need for heat, unlike traditional processes based on thermal energy [1–3].
The main advantages of ADM
Energy efficiency
By exclusively harnessing kinetic energy, ADM operates at room temperature, eliminating the need for heating or thermal consolidation. The energy consumption is significantly reduced compared to traditional sintering methods and deposition processes such as physical vapor deposition (PVD), chemical vapor deposition (CVD), thermal spraying, or liquid-phase processes. This greater energy efficiency results in an estimated reduction in energy consumption of between 50% and 82% [4].
Minimal vacuum conditions
L'ADM se distingue par sa capacité à opérer à pression quasi-atmosphérique ou en conditions de vide brut (1 mbar ou légèrement inférieure), sans nécessiter de vide poussé ou ultra-poussé. Cette simplicité opératoire en fait une solution accessible, économiquement avantageuse et aisément adaptable à des environnements industriels variés, contrairement aux procédés en phase vapeur, qui nécessitent des infrastructures complexes et coûteuses pour atteindre ces niveaux de vide nécessaires [5].
Reduced consumption and low gas pressure
Aerosol Deposition Method (ADM) uses gas pressures close to atmospheric pressure (< 2.5 bars), limiting resource consumption and simplifying equipment sizing. In contrast, processes like Cold Spray require very high pressures (up to 50 bars), temperatures reaching 1100°C, and significant consumption of compressed or inert gases, which increases operational and logistical costs [5].
Preservation of native material and substrate properties
Thanks to the absence of high temperatures, ADM preserves the chemical, crystallographic, and microstructural integrity of the deposited materials. This preservation is particularly beneficial for materials that may have their properties degraded by conventional thermal processes. ADM allows for the deposition of coatings with specific and functional properties such as corrosion resistance, wear resistance, good electrical conductivity, as well as piezoelectric and optical properties. Moreover, this process enables the treatment of a wide variety of substrates, including fragile materials, without the risk of thermal shock or deformation [6].
Immediate densification and consolidation
ADM allows for the creation of densified coatings (> 95% of theoretical density) immediately upon deposition, without requiring a post-consolidation thermal step. This high density ensures optimal mechanical properties and superior functional performance compared to many other processes, which are often limited by insufficient densification. Moreover, for certain materials, especially composites, the density can be modulated to some extent. This modulation, although limited, opens up possibilities for applications that require controlled porosity or specific properties [7].
Moderate deposition growth kinetics
ADM offers a moderate deposition growth rate (between 0.1 and 10 µm/min), typically higher than that of vapor-phase processes, which can only achieve a few nanometers per minute, but lower than that of thermal spraying, which can produce thick deposits in just a few seconds.
Versatility of substrates and thickness
ADM offers unique flexibility, allowing deposition on a variety of substrates such as metals, polymers, ceramics, and composites. It is also suitable for flexible or thin substrates (> 80 µm) and allows the modulation of coating thicknesses between thin layers (≳ 0.7 µm) and thick layers (> 100 µm and ≲ 500 µm) to meet various functional and protective needs.
Technological versatility
Approaching the well-understood and widely studied phenomenological principles of thermal spraying processes, ADM is a technology that can be easily combined with these processes to leverage its intrinsic advantages, improve coating formation quality and efficiency, and expand the possibilities in terms of thickness [4]. This constitutes an active area of research at CTTC in collaboration with Institut de Recherche sur les Céramiques –IRCER [8].
Environmental respect
Without the need for high-pressure compressed gases or excessive heat, ADM has a reduced carbon footprint and minimizes greenhouse gas emissions. Compared to vapor-phase or thermal processes that use toxic or polluting chemicals, ADM is an eco-friendly technology that meets the growing demands for industrial sustainability.
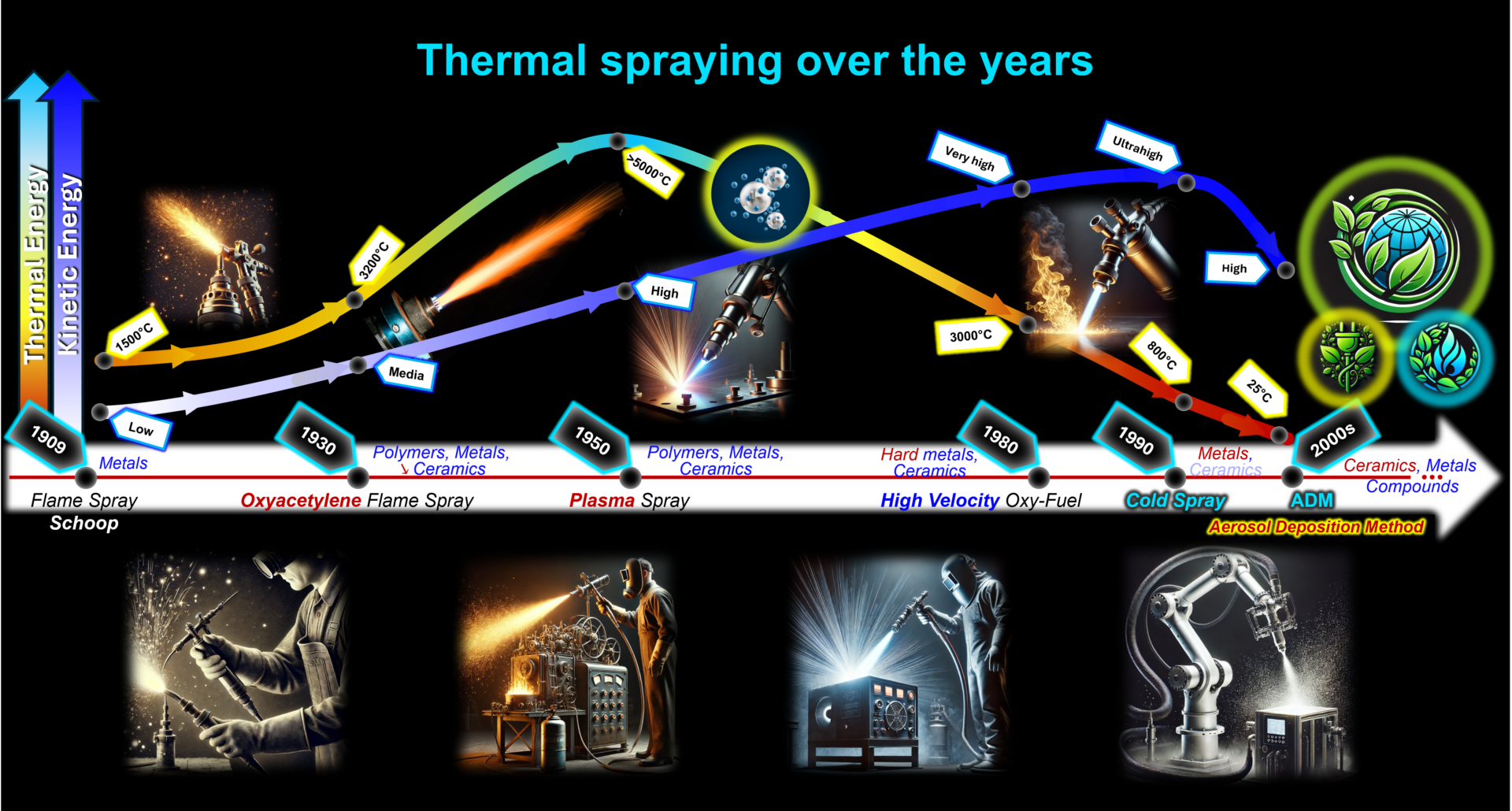
Bibliographic References
[1] J. Akedo, Aerosol deposition of ceramic thick films at room temperature: Densification mechanism of ceramic layers, in: Journal of the American Ceramic Society, 2006: pp. 1834–1839. https://doi.org/10.1111/j.1551-2916.2006.01030.x.
[2] D. Hanft, J. Exner, M. Schubert, T. Stöcker, P. Fuierer, R. Moos, An overview of the Aerosol Deposition method: Process fundamentals and new trends in materials applications, Journal of Ceramic Science and Technology 6 (2015) 147–181. https://doi.org/10.4416/JCST2015-00018.
[3] J. Akedo, Room temperature impact consolidation and application to ceramic coatings: Aerosol deposition method, Journal of the Ceramic Society of Japan 128 (2020) 101–116. https://doi.org/10.2109/jcersj2.19196.
[4] K. Shinoda, H. Noda, K. Ohtomi, T. Yamada, J. Akedo, Promotion of knowledge and technology transfer towards innovative manufacturing process: Case study of new hybrid coating process, International Journal of Automation Technology 13 (2019) 419–431. https://doi.org/10.20965/ijat.2019.p0419.
[5] A. Vardelle, C. Moreau, J. Akedo, H. Ashrafizadeh, C.C. Berndt, J.O. Berghaus, M. Boulos, J. Brogan, A.C. Bourtsalas, A. Dolatabadi, M. Dorfman, T.J. Eden, P. Fauchais, G. Fisher, F. Gaertner, M. Gindrat, R. Henne, M. Hyland, E. Irissou, E.H. Jordan, K.A. Khor, A. Killinger, Y.C. Lau, C.J. Li, L. Li, J. Longtin, N. Markocsan, P.J. Masset, J. Matejicek, G. Mauer, A. McDonald, J. Mostaghimi, S. Sampath, G. Schiller, K. Shinoda, M.F. Smith, A.A. Syed, N.J. Themelis, F.L. Toma, J.P. Trelles, R. Vassen, P. Vuoristo, The 2016 Thermal Spray Roadmap, Journal of Thermal Spray Technology 25 (2016) 1376–1440. https://doi.org/10.1007/s11666-016-0473-x.
[6] C. Lee, M.Y. Cho, M. Kim, J. Jang, Y. Oh, K. Oh, S. Kim, B. Park, B. Kim, S.M. Koo, J.M. Oh, D. Lee, Applicability of Aerosol Deposition Process for flexible electronic device and determining the Film Formation Mechanism with Cushioning Effects, Sci Rep 9 (2019). https://doi.org/10.1038/s41598-019-38477-y.
[7] J. Akedo, Room temperature impact consolidation (RTIC) of fine ceramic powder by aerosol deposition method and applications to microdevices, Journal of Thermal Spray Technology 17 (2008) 181–198. https://doi.org/10.1007/s11666-008-9163-7.
[8] M. Shahien, M. Suzuki, K. Shinoda, J. Akedo, Ceramic Coatings Deposited from Fine Particles by Different Spraying Processes, Journal of Thermal Spray Technology 29 (2020) 2033–2047. https://doi.org/10.1007/s11666-020-01095-6.