Industrial Perspectives of ADM
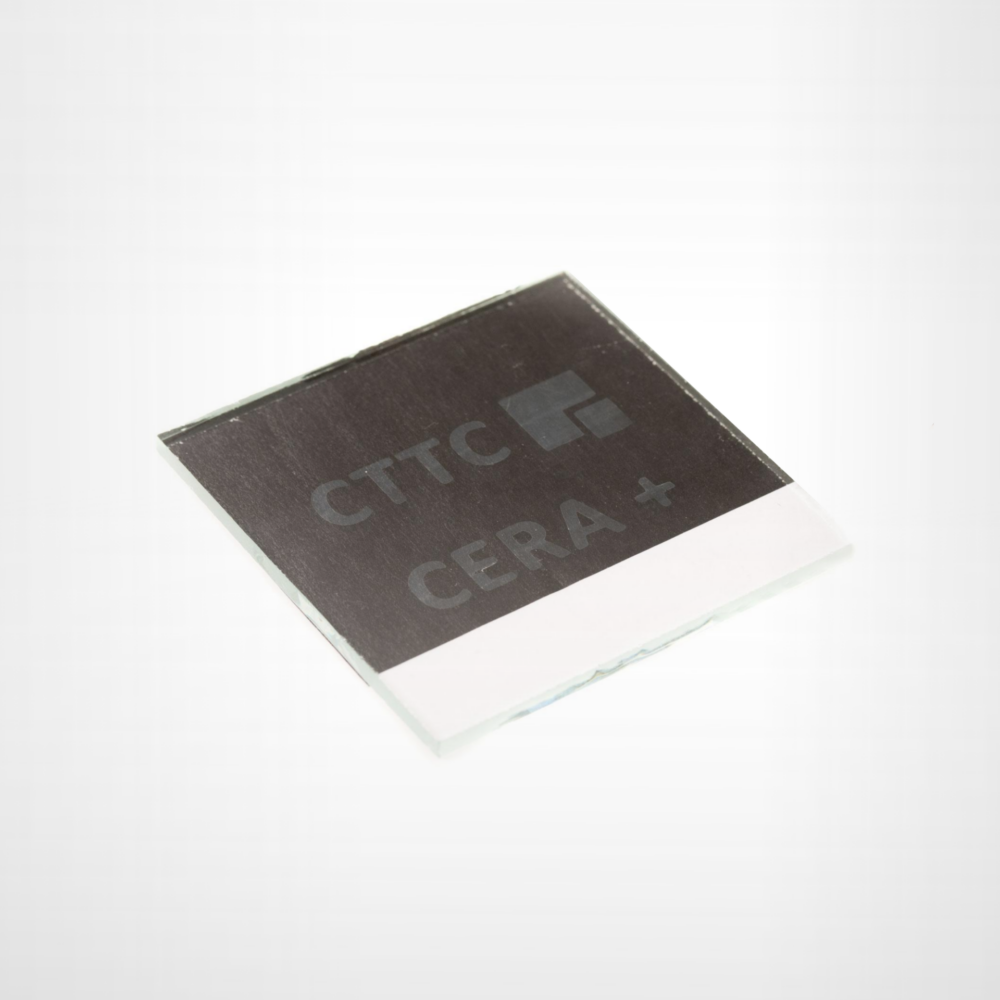
26 Mar 25
Articles
Reading time: 8 minutes
This week, the conclusion of our series on ADM with industrial perspectives.
The Importance of Ceramic Coatings in Industry
Surface coatings play a fundamental role in various industrial fields by providing specific functionalities to materials, making them suitable for demanding applications [1]. Ceramic coatings are particularly used in:
✔️Corrosion protection. They are used to protect metal substrates from corrosion caused by exposure to air, water, or other corrosive agents at high or ambient temperatures.
✔️Enhancing wear resistance. Ceramic coatings extend the durability of materials exposed to friction, abrasion, or other forms of wear.
✔️Electrical or thermal insulation. They provide electrical or thermal insulation to prevent unwanted electricity conduction or regulate heat transfer.
✔️Aesthetic enhancement. Some coatings serve purely aesthetic purposes, improving the appearance of objects or substrates in terms of color, texture, opacity, and more.
✔️Functionalization. Other ceramic coatings exhibit specific properties such as hydrophobicity, antimicrobial activity, bioactivity/biocompatibility, or piezoelectricity, among others.
Among the most well-known coating technologies (Atmospheric/Suspension Plasma Spray – APS/SPS; Cold Spray – CS; Physical/Chemical Vapor Deposition – PVD/CVD), Aerosol Deposition Method (ADM) stands out as an innovative technique for developing ceramic and composite coatings (ceramic-ceramic, ceramic-metal, ceramic-polymer) at room temperature, thus preserving the intrinsic properties of both the deposited materials and the substrates.
This technology enables the production of dense (>95% densification) and adherent (>50 MPa, measured by pull-off test) coatings while ensuring low energy and consumable consumption (carrier gas). These advantages make ADM a promising alternative compared to the technologies presented in the table below.
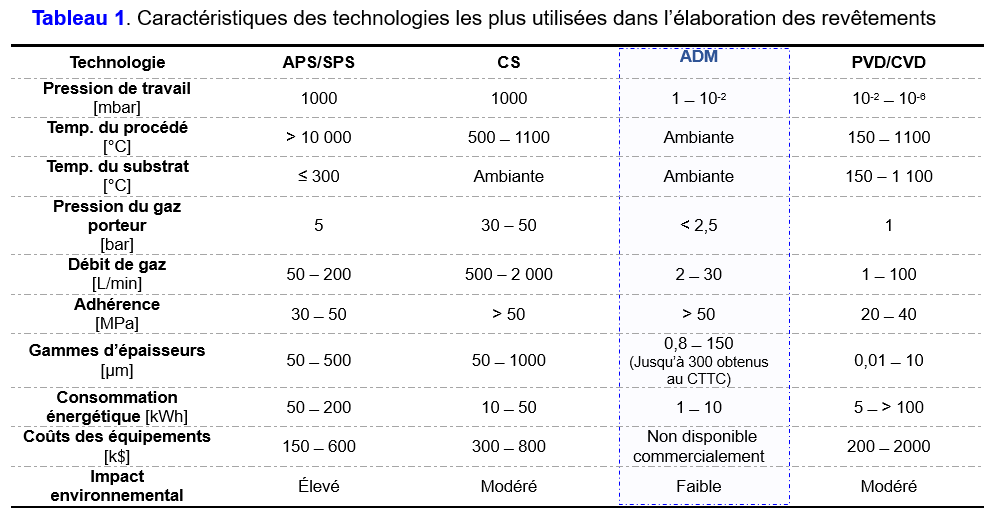
Promising process features
These promising features of the ADM process have led to its use for forming coatings from a variety of materials, such as:
- PZT (lead titano-zirconates)
- Al2O3 (Alumina)
- YSZ (yttria-stabilized zirconia)
- BaTiO3 (Barium titanate)
- AlN (Aluminum nitride)
- Precious metals
- SiC (Silicon carbide)
- MgB2 (Magnesium diboride)
- Phases MAX (Ti3SiC2)
- Composites : LSM-YSZ, Al2O3-PTFE (Alumina - Teflon), TiO2-Cu (Titanium dioxide - Copper), SiC-MoSi2 (Silicon carbide - Molybdenum disilicide)
The industrial sectors in which ADM can have a major impact are as follows:
Electronics and semiconductor devices
ADM can be used to manufacture dielectric, conductive or semiconducting layers, as well as thermal or corrosion protection coatings for electronic devices. Authors such as J. Akedo [2] have produced PZT coatings using the ADM process, improving the material's remanent polarization and dielectric conductivity. These properties are important for the manufacture of microelectromechanical systems (MEMS).
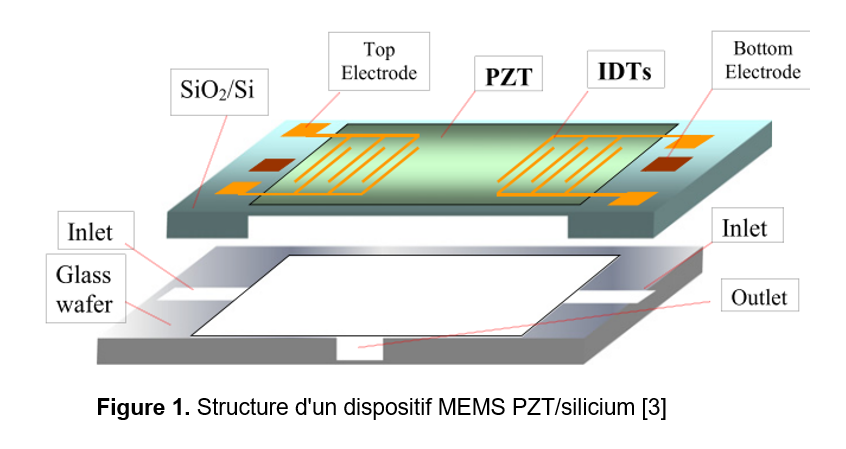
ChatGPT a dit :
Optical Sensors and Devices
It is feasible to develop transparent coatings that provide thermal, corrosive, and erosive protection for optical lenses, devices, and sensors. Researchers such as Jun Akedo and Yuuki Sato have produced transparent PZT (Lead Zirconate Titanate) and Al₂O₃ (Alumina) coatings using the Aerosol Deposition Method (ADM). These coatings exhibit notable properties, including high transmittance and wear resistance, making them suitable for applications in lenses and lasers.

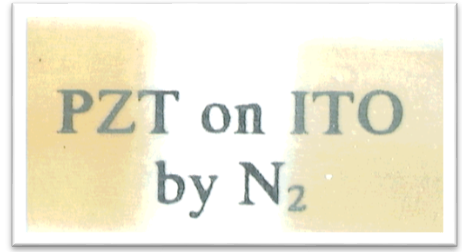
Energy
Fabrication of solid electrodes and electrolytes [6] for the miniaturization of solar cells (rigid or flexible: Figure 5, [7]) and for the development of energy storage devices, such as batteries or supercapacitors. R. Inada et al. [8] used the ADM process to manufacture LAGP (Li1.5Al0.5Ge1.5(PO4)3) electrodes on stainless steel. The results showed that the LAGP coatings maintained their electrical conductivity properties.
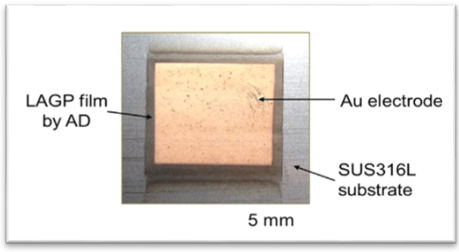
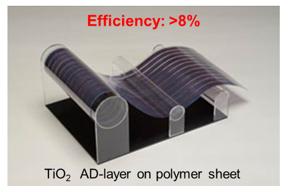
Microelectronics and Microsystems
Fabrication of microdevices, integrated circuits, and electromagnetic layer deposits. ADM allows for the deposition of materials such as ferrites [9], used in smartphones. Due to its electromagnetic properties, this material is used in mobile phones for NFC (Near-field communication) applications based on radio frequency identification technology. Hyung-Jun Kim et al. successfully deposited Ni-Zn-Cu ferrite on glass and polymer substrates, achieving thicknesses of up to 80µm.
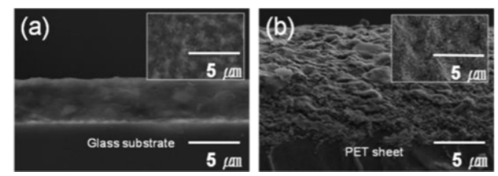
Medical devices
Development of biocompatible coatings on implantable medical devices and the development of protective layers. Udo R. Eckstein et al. [10] created bioactive glass coatings (45S5 Bioglass®) on glass and Ti6Al4V substrates. These coatings showed biocompatibility, as well as adequate cell viability and proliferation. Other authors have also developed hydroxyapatite coatings, a well-studied material for orthopedic applications [11,12].
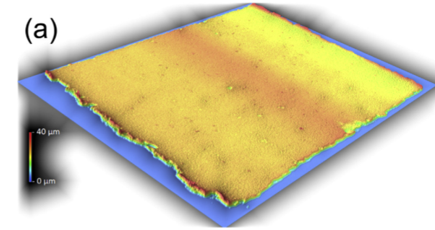
Aerospace
In the aerospace sector, ADM presents a significant interest for various applications mentioned previously, such as the coating of sensors or electronic devices. The process also offers a particularly interesting solution for the creation of thermal barriers, also known as Environmental Barrier Coatings (EBCs). Toshiki Shibuya et al. [13] deposited mullite layers, one of the main components of EBCs, on glass, alumina, and silicon substrates. The coatings obtained have the same chemical composition and phase as raw mullite.
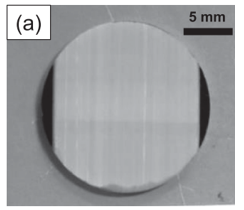
Ceramics sector
Development of functional coatings for wear resistance, corrosion, impact, or aesthetic reasons. H. Noda and J. Akedo [7] successfully deposited colored resins on ceramic substrates for aesthetic applications in smartphones. This allowed them to reduce the weight of the mobile phone support while maintaining the characteristics of its surface. Kentaro Shinoda et al. [14] studied the possibility of coating cooking pans with alumina using the 'Hybrid Aerosol Deposition' technique. This new approach also highlights the potential to achieve three-dimensional coatings through the HAD method.
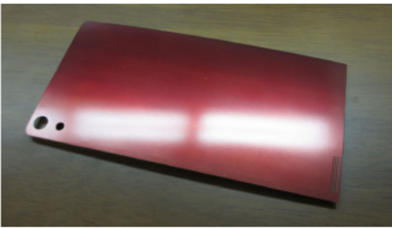
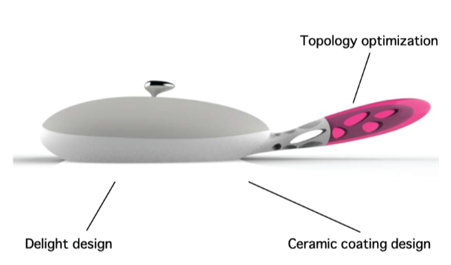
Our previous articles on ADM
Bibliographic references
[1] A.S.M. Ang, N. Sanpo, M.L. Sesso, S.Y. Kim, C.C. Berndt, Thermal spray maps: Material genomics of processing technologies, Journal of Thermal Spray Technology 22 (2013) 1170–1183. https://doi.org/10.1007/s11666-013-9970-3.
[2] J. Akedo, M. Lebedev, S. Baba, Aerosol deposition method for preparation of lead zirconate titanate thick layer at low temperature-improvement of electrical properties by irradiation of fast atom beam and plasma-, Japanese Journal of Applied Physics, Part 1: Regular Papers and Short Notes and Review Papers 42 (2003) 5931–5935. https://doi.org/10.1143/jjap.42.5931.
[3] K. Uchino, Glory of piezoelectric perovskites, Sci Technol Adv Mater 16 (2015). https://doi.org/10.1088/1468-6996/16/4/046001.
[4] Y. Sato, Y. Uemichi, K. Nishikawa, S. Yoshikado, Fabrication of Al2O3 films using aerosol deposition method and their characterization, in: IOP Conf Ser Mater Sci Eng, Institute of Physics Publishing, 2011. https://doi.org/10.1088/1757-899X/18/9/092056.
[5] J. Akedo, M. Lebedev, Influence of Carrier Gas Conditions on Electrical and Optical Properties of Pb(Zr, Ti)O 3 Thin Films Prepared by Aerosol Deposition Method, 2001. http://iopscience.iop.org/1347-4065/40/9S/5528.
[6] X. Wang, R.A. Paredes Camacho, X. Xu, Y. Wang, Y. Qiang, H. Kungl, R.A. Eichel, Y. Zhang, L. Lu, Aerosol deposition technology and its applications in batteries, Nano Materials Science (2023). https://doi.org/10.1016/j.nanoms.2023.11.002.
[7] J. Akedo, Room temperature impact consolidation and application to ceramic coatings: Aerosol deposition method, Journal of the Ceramic Society of Japan 128 (2020) 101–116. https://doi.org/10.2109/jcersj2.19196.
[8] R. Inada, K. ichi Ishida, M. Tojo, T. Okada, T. Tojo, Y. Sakurai, Properties of aerosol deposited NASICON-type Li1.5Al0.5Ge1.5(PO4)3 solid electrolyte thin films, Ceram Int 41 (2015) 11136–11142. https://doi.org/10.1016/j.ceramint.2015.05.062.
[9] H.J. Kim, O.Y. Kwon, C.I. Jang, T.K. Kim, J.R. Oh, Y.J. Yoon, J.H. Kim, S.M. Nam, J.H. Koh, Room-temperature growth of Ni-Zn-Cu ferrite/PTFE composite thick films on PET via aerosol deposition, Electronic Materials Letters 9 (2013) 805–807. https://doi.org/10.1007/s13391-013-6016-4.
[10] U.R. Eckstein, R. Detsch, N.H. Khansur, M. Brehl, U. Deisinger, D. de Ligny, A.R. Boccaccini, K.G. Webber, Bioactive glass coating using aerosol deposition, Ceram Int 45 (2019) 14728–14732. https://doi.org/10.1016/j.ceramint.2019.04.197.
[11] G. Kubicki, V. Leshchynsky, A. Elseddawy, M. Wiśniewska, R.G. Maev, J. Jakubowicz, J. Sulej-Chojnacka, Microstructure and Properties of Hydroxyapatite Coatings Made by Aerosol Cold Spraying–Sintering Technology, Coatings 12 (2022). https://doi.org/10.3390/coatings12040535.
[12] P. Parajuli, Dense Coating of Hydroxyapatite Particles Over Titanium Alloy by Dense Coating of Hydroxyapatite Particles Over Titanium Alloy by Aerosol deposition Method Aerosol deposition Method, 2019. https://digitalcommons.memphis.edu/etd.
[13] T. Shibuya, T. Mizuno, A. Iuchi, M. Hasegawa, Formation of mullite coating by aerosol deposition and microstructural change after heat exposure, Mater Trans 61 (2020) 540–547. https://doi.org/10.2320/matertrans.MT-M2019354.
[14] K. Shinoda, H. Noda, K. Ohtomi, T. Yamada, J. Akedo, Promotion of knowledge and technology transfer towards innovative manufacturing process: Case study of new hybrid coating process, International Journal of Automation Technology 13 (2019) 419–431. https://doi.org/10.20965/ijat.2019.p0419.