L'Aerosol Deposition Method (ADM)
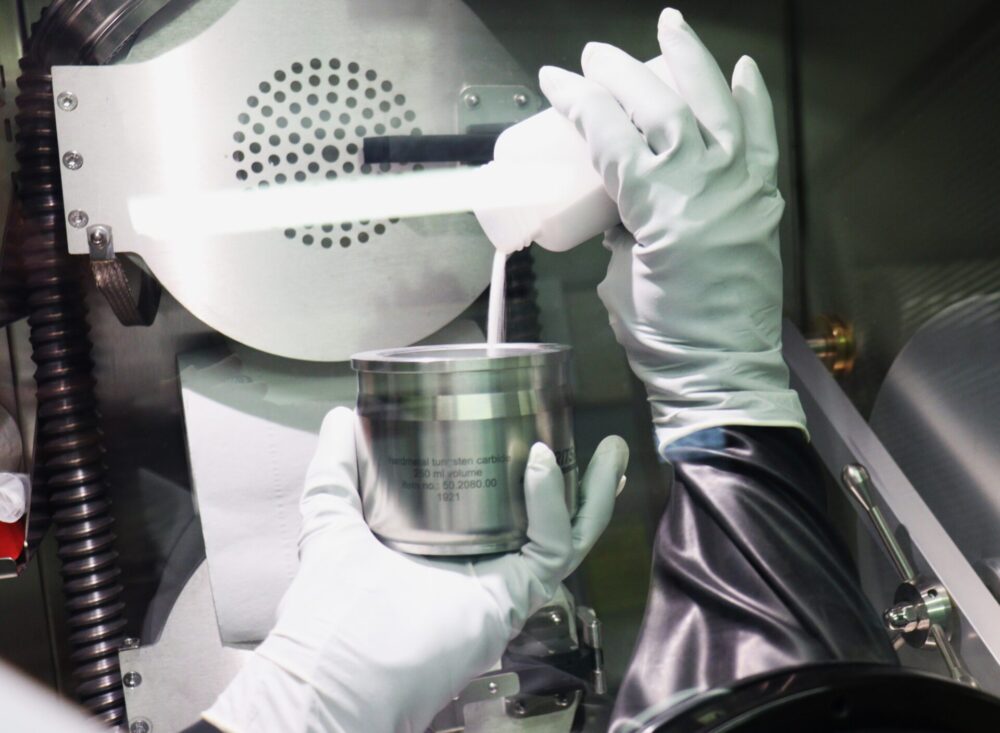
22 Jan 25
Articles
Temps de lecture : 16 minutes
The Aerosol Deposition Method (ADM) is an innovative technology for ceramic coatings with a low environmental impact.
Coatings and Surface Engineering: An Introduction to the Aerosol Deposition Method
Coatings play a crucial role in enhancing the properties of materials and surfaces. They meet high-performance requirements in often extreme environments. In particular, ceramic coatings, due to their exceptional properties, provide solutions tailored to the most demanding environments. This includes improvements in mechanical, thermal, and chemical properties. In sectors such as aerospace, energy, and the medical industry, they protect surfaces from wear, corrosion, and heat. They also impart specific functionalities. These coatings are often critical in ensuring the performance and durability of components.
To meet these needs, various deposition technologies have been developed over time. Vapor phase processes, although precise, require expensive infrastructure and high vacuum conditions, even ultra-high vacuum (>10-8 mbar). Liquid phase processes, which are simpler, are limited by the low density of the deposits and are energy-intensive. These limitations have made thermal spraying one of the most widely used techniques. It is valued for its versatility and performance in many industrial applications. However, even within this technology, alternatives have emerged to address energy challenges and expand application fields.
Since its invention in 1909 by Schoop, primarily for metal deposition, thermal spraying has gradually evolved. It now allows for the deposition of ceramics and composites by utilizing energy sources such as plasma or electric arcs. This technology has transformed coating manufacturing by combining versatility and performance. However, it still relies on high energy inputs. The heat required to melt or semi-melt the particles leads to significant resource consumption and often causes chemical and structural alterations of materials, compromising their functional properties. Over time, efforts have been made to reduce this dependence on thermal energy, favoring kinetic energy instead. This has led to the development of technologies like Cold Spray. This method minimizes thermal degradation by projecting particles at high speed without melting them. However, to achieve these high speeds, it is necessary to use very high pressures and significant gas consumption. Additionally, this method remains limited to ductile materials, leaving pure ceramics outside of these advancements. However, they can be co-deposited with metals, as is now the case (cf. Figure 1).
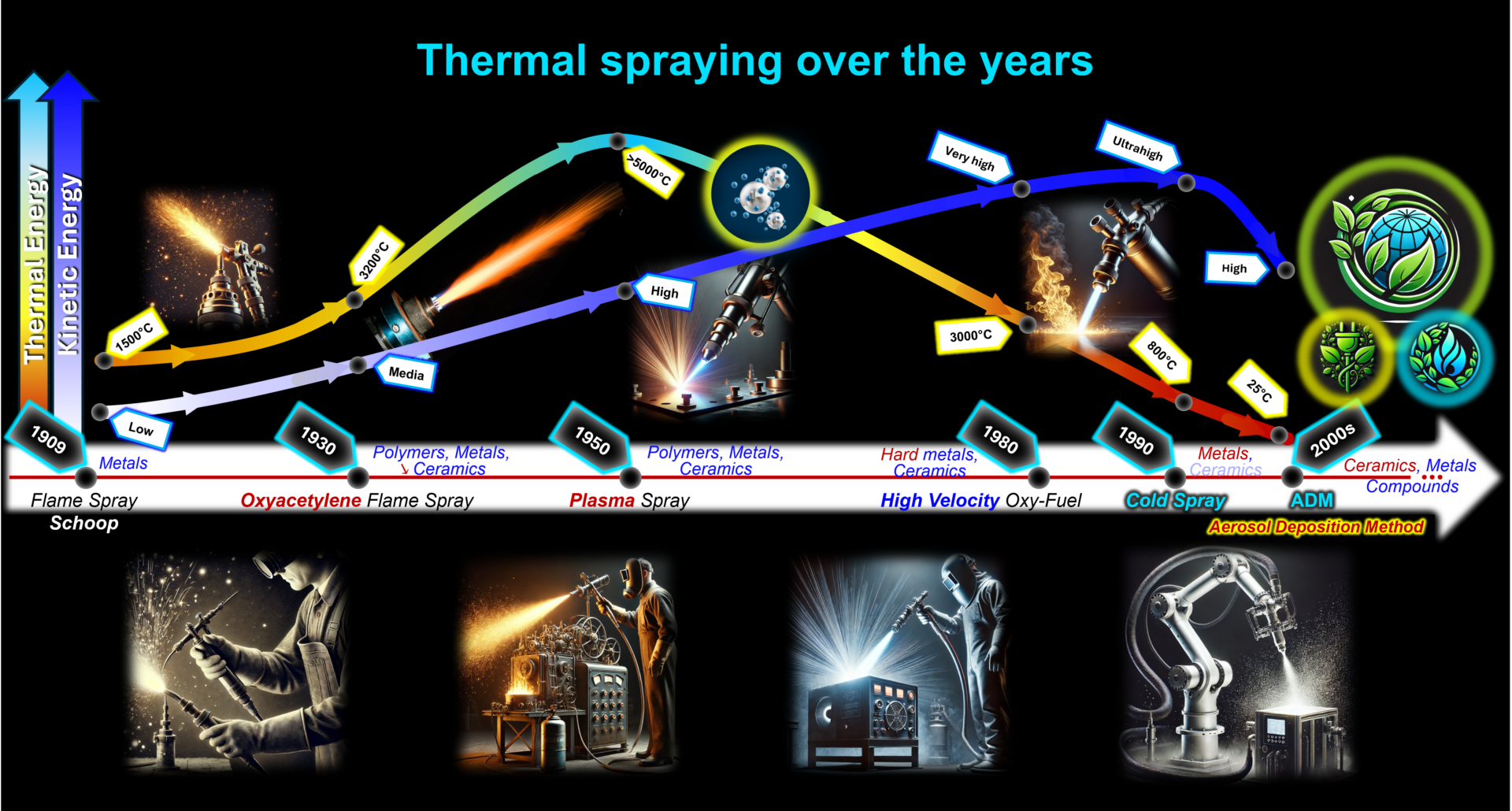
The evolution of industrial needs and environmental constraints today calls for a rethinking of coating technologies. The goal is to reduce energy consumption, carbon footprint, and the use of gases while maintaining high performance. The Aerosol Deposition Method (ADM) technology, although recent, is gradually establishing itself as a promising solution. By exclusively harnessing kinetic energy, it allows for the deposition of ceramics, composites, and even metals at room temperature. This applies to a wide range of substrates (rigid, flexible, thin, or thick), thus avoiding thermal constraints while offering a simple, effective, and environmentally friendly alternative.
As an innovative method, ADM is not only intended to replace certain applications of existing technologies. It can also complement them, offering hybrid solutions tailored to complex issues. ADM is part of the legacy of phenomenological and technological advances in thermal spraying. It overcomes energy and environmental constraints, thus opening the door to new industrial opportunities.
What is ADM?
The Aerosol Deposition Method (ADM) is an innovative coating deposition technique. It is primarily characterized by the formation of dense (>95%) and nanostructured films directly at room temperature. Unlike traditional processes based on thermal energy, ADM exclusively utilizes kinetic energy to consolidate particles. It requires no melting or annealing, thus preserving the intrinsic properties of the deposited materials.
This method uses dry solid particles suspended in a dry carrier gas (compressed air, O2, N2, He, Ar, or mixtures). It relies on the high-speed impact (100–600 m/s) of these particles onto a substrate. This results in a series of complex mechanical phenomena such as plastic deformation, cracking, and fragmentation. At the nanometric scale, ceramics exhibit pseudo-plasticity, facilitating their deformation under stress. Metals, naturally ductile, undergo mechanical deformations amplified by these same stresses. These mechanisms lead to the creation of new, highly reactive surfaces, which together enhance adhesion, consolidation, and densification of the layers forming the coating.
ADM has its origins in the 1990s in Japan. Researchers, drawing on advances in solid-state physics, explored the submicron/nanometric scale plasticity of ceramics. This phenomenon is also present in metals as amplified localized deformation. This discovery paved the way for a method capable of depositing ceramics, as well as metals and composites. These composites include ceramic-metal and ceramic-polymer, which are suitable for a wide variety of substrates.
The main advantages of ADM include:
✔️ Energy efficiency: By exclusively exploiting kinetic energy, ADM operates at room temperature, eliminating the need for heating or thermal consolidation. This significantly reduces energy consumption compared to thermal spraying or liquid-phase processes.
✔️ Minimal vacuum conditions: ADM stands out for its ability to operate at near-atmospheric pressure or in rough vacuum conditions (1 mbar or slightly lower). It does not require high or ultra-high vacuum. This operational simplicity makes it an accessible, cost-effective solution that can be easily adapted to various industrial environments. Unlike vapor-phase processes, it does not require complex and expensive infrastructure to achieve the necessary vacuum levels.
✔️ Reduced consumption and low gas pressure: ADM operates with gas pressures close to atmospheric pressure (< 2.5 bar). This limits resource consumption and simplifies equipment sizing. In contrast, processes like Cold Spray require very high pressures (up to 50 bar) and extremely high temperatures, which can reach 1100°C. These processes consume significant amounts of compressed or inert gas, increasing operational and logistical costs.
✔️ Preservation of material and substrate properties: Thanks to the absence of high temperatures, ADM maintains the chemical integrity of the deposited materials. It also preserves their crystallographic and microstructural structure. This preservation is particularly beneficial compared to materials that can be degraded by thermal processes. Additionally, ADM allows for the processing of a wide variety of substrates, including fragile materials, without the risk of thermal deformation.
✔️ Immediate densification and consolidation: ADM allows for the production of dense coatings (> 95% of theoretical density) immediately upon application, without the need for thermal consolidation. This high density ensures optimal mechanical properties and superior functional performance. It surpasses many other processes, which are often limited by insufficient densification. Additionally, for certain materials, particularly composites, the density can be modulated to some extent. This flexibility, though limited, opens up possibilities for applications requiring controlled porosity or specific properties.
✔️ Moderate deposition growth kinetics: ADM offers a deposition growth rate (between 0.1 and 10 µm/min), which is generally higher than that of vapor-phase processes. These can only reach a few nanometers per minute, but it is slower than thermal spraying, which can produce thick deposits in just a few seconds.
✔️ Substrate and thickness versatility: ADM offers unique flexibility, allowing deposition on a variety of substrates such as metals, polymers, ceramics, and composites. It is also suitable for flexible or thin substrates (> 80 µm). It enables the modulation of coating thicknesses, ranging from thin layers (≳ 0.7 µm) to thick layers (> 100 µm and ≲ 500 µm). This versatility meets various functional and protective needs.
✔️Environmental respect: With no need for high-pressure compressed gases or excessive heat, ADM has a reduced carbon footprint. It also minimizes greenhouse gas emissions. Compared to vapor-phase or thermal processes, it is an environmentally responsible technology. It thus meets the growing demands for industrial sustainability.
The ADM system (see Figure 2) mainly consists of three components: an aerosol generator (AG), a deposition chamber (CR), and a pumping system. The process begins with the formation of an aerosol in the AG, where dry particles are suspended. This is done by injecting a carrier gas (such as N₂, He, Ar, or dry compressed air) and applying a vibrational effect. The pressure difference between the AG and the CR allows the particles to be transported through a nozzle. They are accelerated before being projected onto the substrate to form the deposit. The absence of sintering or subsequent thermal treatment reduces energy consumption while minimizing environmental impact.
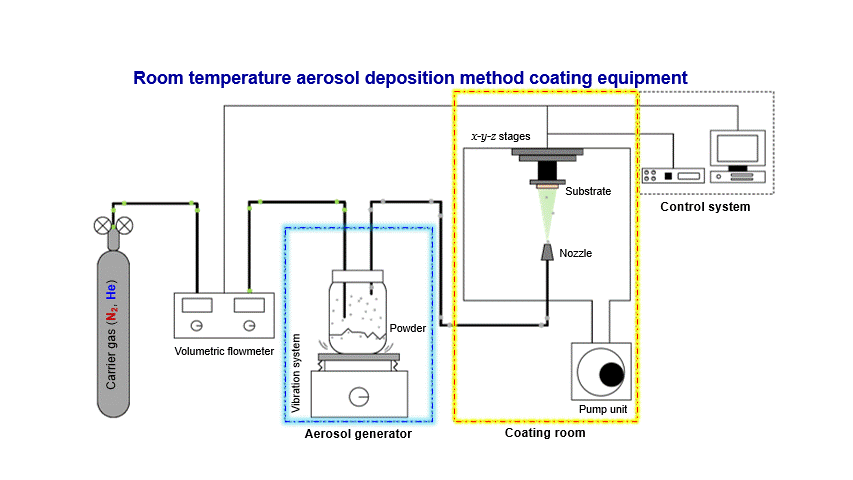
Fundamental Principles of Coating Formation by ADM
The Aerosol Deposition Method (ADM) is based on complex physicochemical phenomena that allow ceramic particles to be consolidated at room temperature. This process, described by Jun Akedo under the concept of Room Temperature Impact Consolidation (RTIC), is widely recognized by the scientific community. Through numerous studies and the expertise of the CTTC, a chronological sequence of key steps has been established, ranging from aerosol generation to coating formation.
✔️ Generation and Acceleration of Particles: Ceramic particles, ranging in size from 0.1 to 5 µm, are suspended in a carrier gas under low pressure (0.1–0.25 MPa), forming a stable aerosol. These particles, propelled through a supersonic nozzle, reach speeds of 100 to 600 m/s, accumulating enough kinetic energy to initiate consolidation upon impact with the substrate.
✔️Initial Impact on the Substrate: Upon impact, the particles exert very high local pressures, ranging from 1 to 15 GPa, for a few nanoseconds. These stresses cause rapid fragmentation of the particles, generating nanometric fragments with reactive surfaces and free bonds, thereby increasing their surface energy. Simultaneously, the impact leads to erosion of the substrate, creating local roughness that enhances mechanical adhesion.
✔️ Local Plasmas and Fracture Emission: The impact of high-speed particles causes fragmentation and erosion of the substrate, breaking chemical bonds and releasing electrons, ions, and reactive nanoparticles. These phenomena can lead to the formation of transient plasmas, which may chemically activate the surfaces and promote initial adhesion. Although their exact role in ADM is still not fully studied, they represent an active area of research where the CTTC is making significant contributions to deepening the understanding of these complex mechanisms, in collaboration with Institut de Recherche sur les Céramiques.
✔️ Release and Dissipation of Thermal Energy: A portion of the kinetic energy of the particles is converted into transient heat upon impact, causing a local temperature rise that can reach 200 to 500°C. Although this local heat is quickly dissipated, it helps activate the surfaces and improve adhesion. In the case of metallic substrates, such as aluminum, this thermal energy can also induce localized microdeformations, strengthening the mechanical anchoring.
✔️ Nanometric Fragments and Interaction with the Substrate: The residual fragments resulting from particle fragmentation reorganize to maximize inter-particle contact and enhance local cohesion. The chemical compatibility between the fragments and the substrate promotes the formation of initial chemical bonds, strengthening adhesion. These bonds, often iono-covalent in the case of ceramics, ensure cohesion that is crucial for the subsequent densification stages.
✔️Formation of the First Layer: The fragments generated during the impact chemically and physically interact with the substrate to form an initial layer less than 1 µm thick. This process relies on pseudo-sintering (consolidation), where reactive bonds (Van der Waals, ionic, and/or covalent) between the fragments and the substrate ensure initial consolidation. This layer serves as a stabilizing role, acting as a buffer for subsequent impacts and facilitating the uniform progression of the coating.
✔️Hammering and Densification: The successive impacts of the particles exert additional pressure on the coating, progressively reducing the initial porosity to less than 5%, achieving a relative density greater than 95%. This process is supported by the pseudo-plasticity of ceramics at the nanometric scale, while in metals, plastic deformation contributes to better compaction.
✔️Multilayer Construction: Each new layer deposited interacts mechanically with the previous layers, influencing the overall structure of the coating. This process allows for controlled thicknesses ranging from 1 to 500 µm, tailored to specific applications such as thermal barriers, protective layers, or functional materials for electronics and optics.
Importance of Raw Materials and Kinetic Parameters
The success of the Aerosol Deposition Method (ADM) relies on the rigorous preparation and precise control of raw materials as well as kinetic parameters. These factors, which are key to the process, directly determine the quality of the deposit and the overall efficiency of the method. This is why the CTTC, with over 40 years of experience in ceramic processing and raw material adaptation, has focused its efforts on this aspect. Thanks to the expertise developed over several years in raw material processing for ADM, it has been able to develop suitable materials that not only allow the formation of high-quality coatings but also enable thickness modulation to meet specific needs.
✔️ Particle size. The particle size distribution is a key parameter to ensure stable projection and effective consolidation (see Figure 3):
- Fine particles: Due to their low inertia, they tend to bounce off the substrate, reducing the efficiency of the deposition.
- Coarse particles: They can cause excessive erosion of the substrate and limit the densification of the coating.
- Controlled distribution: An optimized particle size range, between 0.1 and 5 µm, balances inertia and kinetic energy to maximize adhesion and
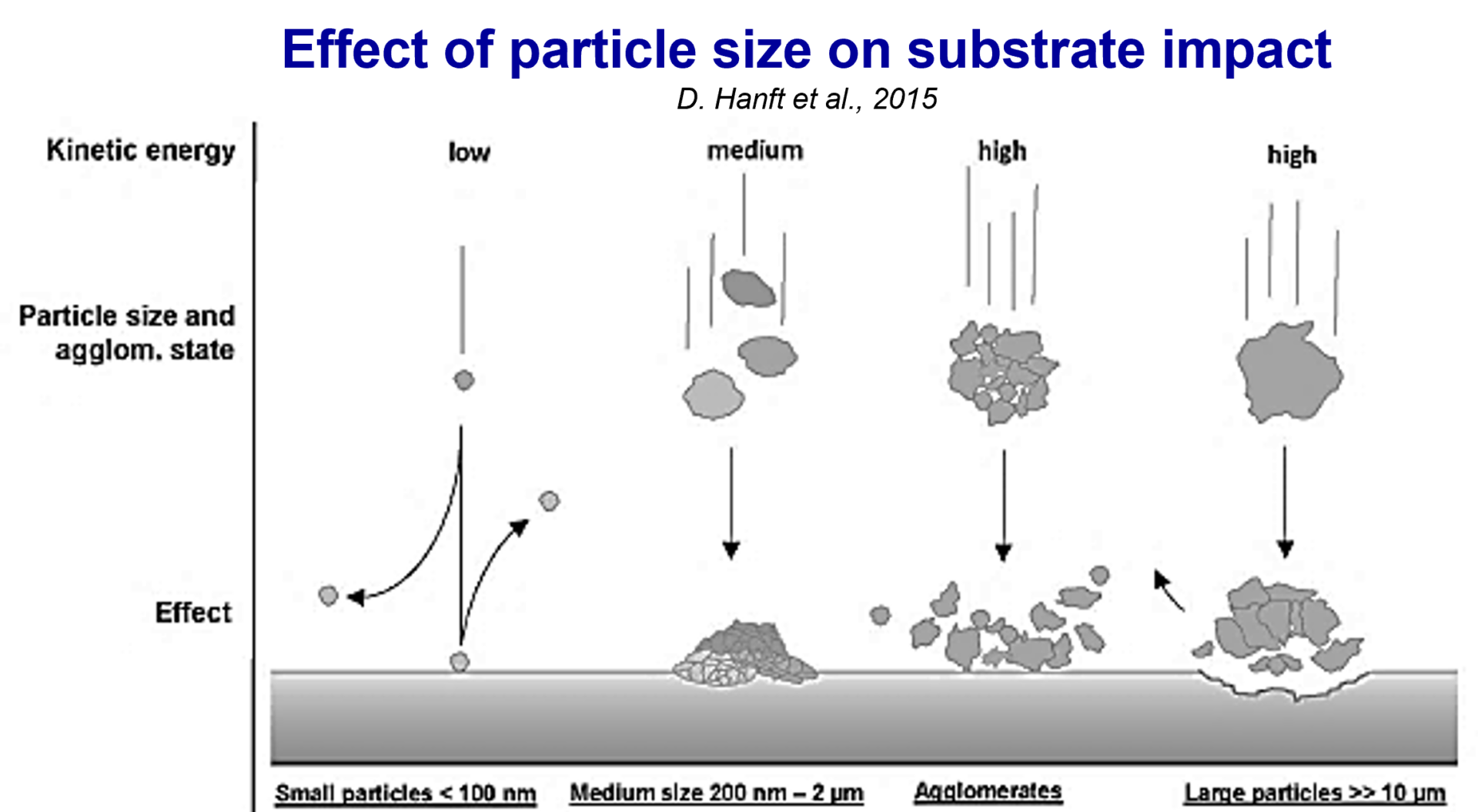
Bibliographic reference:
D. Hanft, J. Exner, M. Schubert, T. Stöcker, P. Fuierer, R. Moos, An Overview of the Aerosol Deposition Method: Process Fundamentals and New Trends in Materials Applications, Journal of Ceramic Science and Technology 6 (2015) 147–182.
✔️ Particle morphology: Spherical or isotropic particles promote a stable trajectory and homogeneous dispersion in the gas flow (see Figure 4). Treatments can be applied to stabilize their aerodynamic behavior.
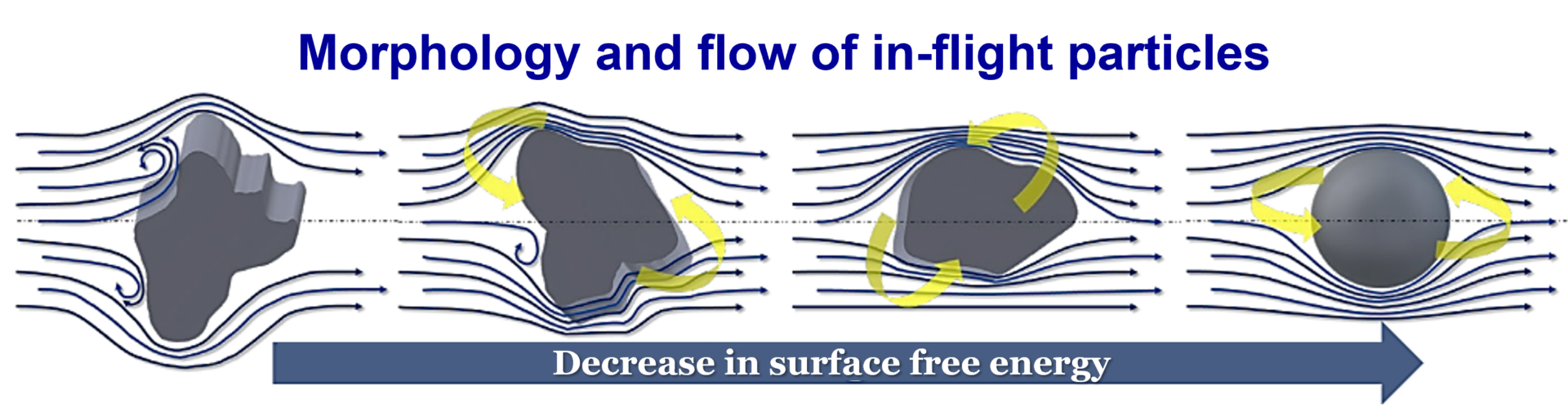
Bibliographic reference:
Contribution to the understanding of porosity formation in bioactive glass coatings and particles fabricated by thermal spraying for biomedical applications, Université de Limoges / Universidad de Antioquia, 2021.
✔️ Critical velocity and kinetic parameters: Each material and particle size has a specific critical velocity that directly influences fragmentation and consolidation. Insufficient velocity can limit adhesion, while excessive velocity may lead to increased erosion or degradation of the substrate structure (see Figure 5).
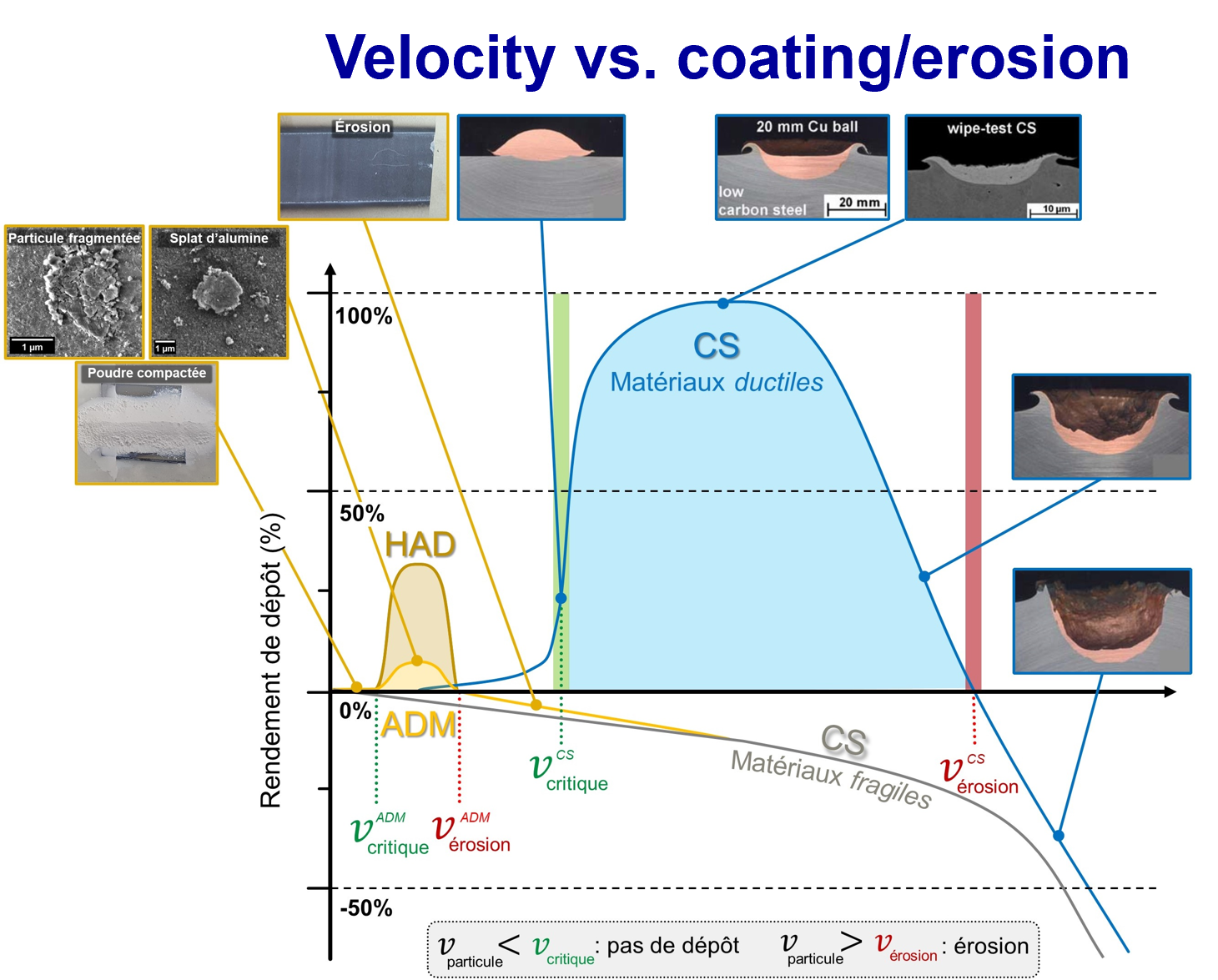
Bibliographic reference:
D. Hanft, J. Exner, M. Schubert, T. Stöcker, P. Fuierer, R. Moos, An Overview of the Aerosol Deposition Method: Process Fundamentals and New Trends in Materials Applications, Journal of Ceramic Science and Technology 6 (2015) 147–182
Applications and innovation
ADM is a versatile technology with applications in various strategic fields, providing innovative solutions for industry.
✔️Electronics: Deposition of conductive and insulating coatings. Manufacture of thin films for microelectronic devices, including piezoelectric materials
✔️ Energy: Production of electrodes for lithium-ion batteries and vibrational energy harvesting devices. Potential applications in supercapacitors due to the ability to deposit composite materials.
✔️ Medical: Biocompatible coatings on medical implants, offering corrosion resistance and antibacterial properties. Development of functional surfaces tailored for prosthetics and implantable devices.
✔️ Optics: Manufacture of transparent coatings for precision optical devices. Protective coatings against wear and scratches for lenses and advanced optical systems.
✔️ Aerospace: Deposition of wear-resistant, corrosion-resistant, and thermally stable protective coatings for critical components. Potential manufacturing of lightweight thermal barriers for turbines and aircraft engines.
Challenges and perspectives.
Despite the numerous advantages offered by ADM, some challenges remain, requiring ongoing research and development efforts.
✔️ Control of operating parameters: Precision in controlling parameters such as particle velocity, gas pressure, and spraying distance remains crucial to ensuring coating quality.
✔️ Material adaptability: Expanding the range of materials compatible with ADM, particularly for polymers and certain advanced composites, is a priority for researchers. This includes the development of specific techniques to process low-density or thermosensitive materials.
✔️ Scale-up: The industrial scale-up of the ADM process requires significant investments in infrastructure and technological optimization. Challenges include designing systems capable of maintaining deposition uniformity on large surfaces or complex geometries
However, these challenges are offset by characteristics that position ADM as a cutting-edge technology and a promising solution for the future. Its ability to produce dense ceramic coatings at room temperature, combined with reduced energy consumption and flexibility in the nature of substrates treated, makes it an environmentally friendly method perfectly aligned with the growing industrial sustainability requirements. Furthermore, recent advancements in powder optimization, the integration of composite materials, and the improvement of deposition kinetics are paving the way for new applications.
With its adaptability and innovation potential, ADM represents more than just a deposition method: it is a strategic technology for developing advanced materials with a low environmental impact, addressing the current and future needs of the most demanding industries.