CERAGREEN 3D
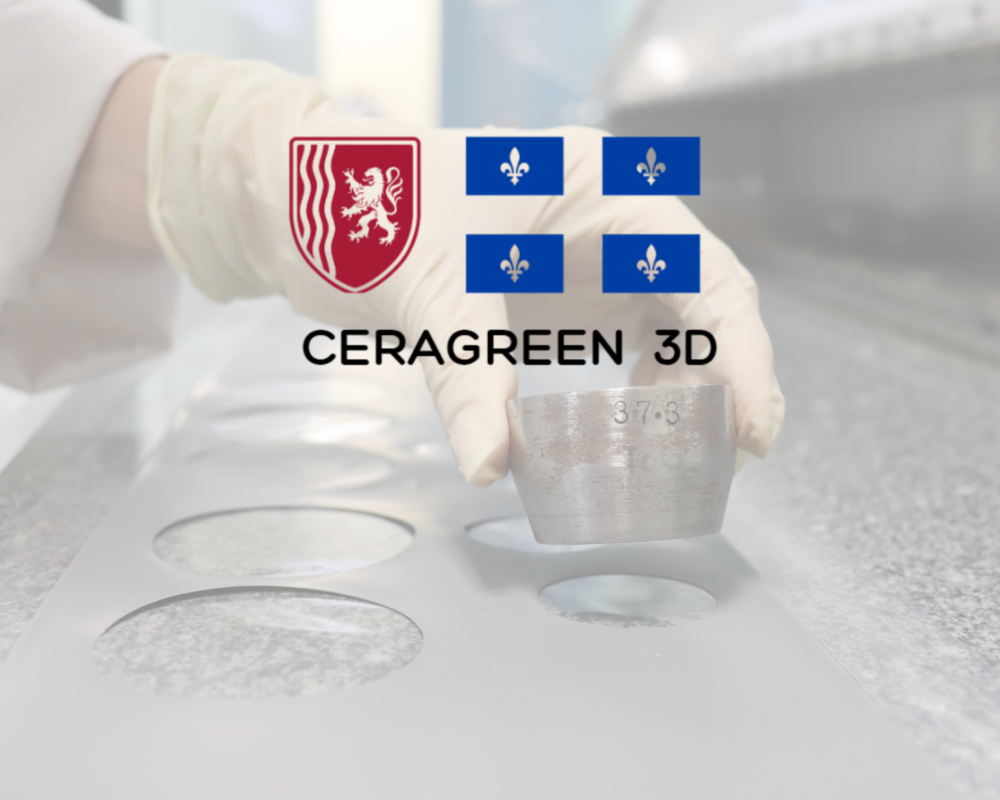
13 Nov 24
Articles
The CERAGREEN 3D project is part of the ADDICERAM project, which is part of the CTTC's CERA 3+ resourcing programme.
The ADDICERAM project is pursuing the development of additive manufacturing technologies for ceramics. These include the binder projection process on a powder bed (CERAJETTING), stereolithography and microdispensing processes for the production of optical components (OPTICERAM). The 3D printing of eco-responsible ceramic feedstocks (CERAGREEN 3D) is also involved.
As part of the CERAGREEN 3D project, the CTTC is working with Canadian partners (COALIA, Université de Sherbrooke, FabLab Inc) to develop biosourced feedstocks suitable for the manufacture of complex-shaped ceramic parts using 3D printing. The main challenge is to reduce the environmental impact of the petroleum-based organic auxiliaries used for formulation, as well as the heat treatments applied after shaping (in particular debinding). The project began in June 2023 and will run until June 2026.
From the choice of raw materials and shaping...
The success of the CERAGREEN 3D project depends initially on the selection of biobased materials and laboratory-scale feedstock preparation trials. Preliminary mixing tests on a sand bath will enable us to observe the behaviour of the various additives with the ceramic powder. In addition, the rheological behaviour of the biobased feedstocks was characterised in order to compare them with commercial materials used as references. The maximum mass of powder incorporated then makes it possible to determine a filler rate that the consortium wishes to maximise in line with the targeted shaping process.
As part of the CERAGREEN 3D project, the team is using the micro-extrusion (or Robocasting) shaping process based on granules (FGF: Fused Granular Fabrication) or filament (FFF: Fused Filament Fabrication).
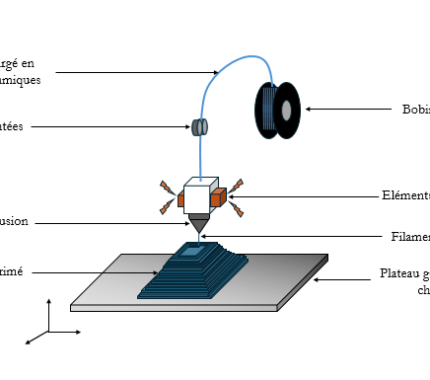
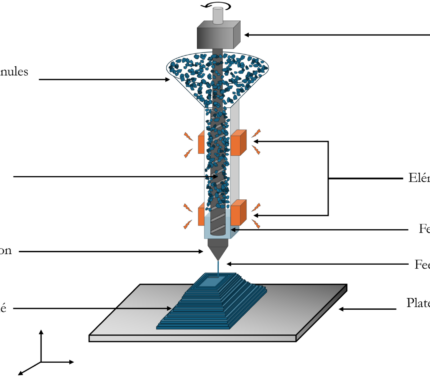
Figure 1: Diagrams of the FFF (a) and FGF (b) processes
Once the feedstock formulation has been validated from a rheological and filler content point of view, it is prepared in larger quantities in appropriate mixers. The feedstock is then crushed and sieved or extruded directly through a die fitted with a rotating knife to obtain calibrated granules.
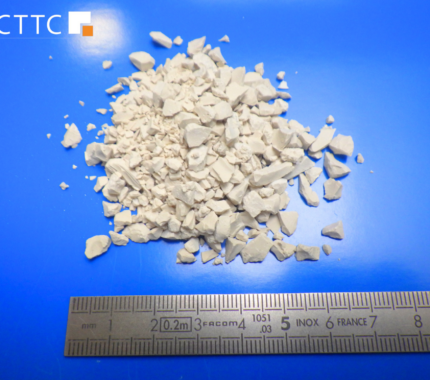
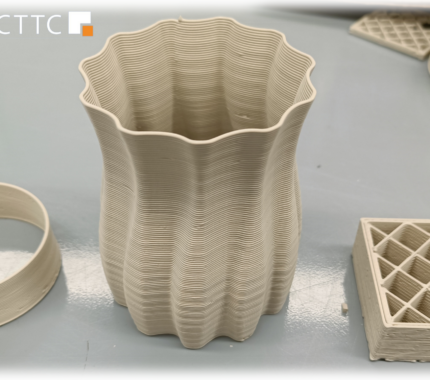
FigFigure 2. Photographs of calibrated granules (left) and examples of ‘green’ parts with different geometries printed by FGF from bio-based feedstock.ure 2. Photographies de granules calibrés (à gauche) et exemples de pièces « vertes » de géométries différentes imprimées par FGF à partir d’un feedstock biosourcé
... to produce eco-responsible end parts.
Once the parts have been shaped, a debinding stage is applied. Unlike what is usually done for ceramic parts (injected, for example) to eliminate the organic additives used via thermal debinding, the CERAGREEN 3D consortium aims to use debinding by extracting the organics using supercritical CO2 (CO2 SC).
Under the right temperature and pressure conditions, CO2 goes into a supercritical state and has characteristics (viscosity in particular) that enable certain organic materials to be partially or even totally extracted/solubilised.
![Figure 3. Diagramme de phase du CO2 [Radwan Chahal. Capteurs optiques en fibres de verre de chalcogénure dopées terres rares appliqués à la surveillance du stockage géologique de CO2. Matériaux. Université de Rennes 1, 2015. Francais.]](https://www.cttc.fr/wp-content/uploads/2024/11/diagramme-de-phase-du-co2.png)
As well as allowing the recovery of the extracted additives, the other advantages of this type of debinding are the treatment time, which is generally shorter than for thermal debinding, and the reduction in greenhouse gas emissions due to the absence of combustion of the organics by oxidation at temperature. CO2 SC also represents an alternative to some of the other organic solvents used (ethanol, acetone, hexane) or to catalytic debinding.
Once the parts have been debonded under optimised conditions, they are sintered and monitored using a range of measurement techniques. The macroscopic and microscopic morphology is analysed mainly by digital microscopy and scanning electron microscopy, also enabling the absence of defects such as microcracks to be checked. The density is determined by hydrostatic weighing to determine the porosity of the samples. As the CERAGREEN 3D project is part of an eco-responsible framework, non-destructive characterisation (NDT) methods are also used to determine certain properties.
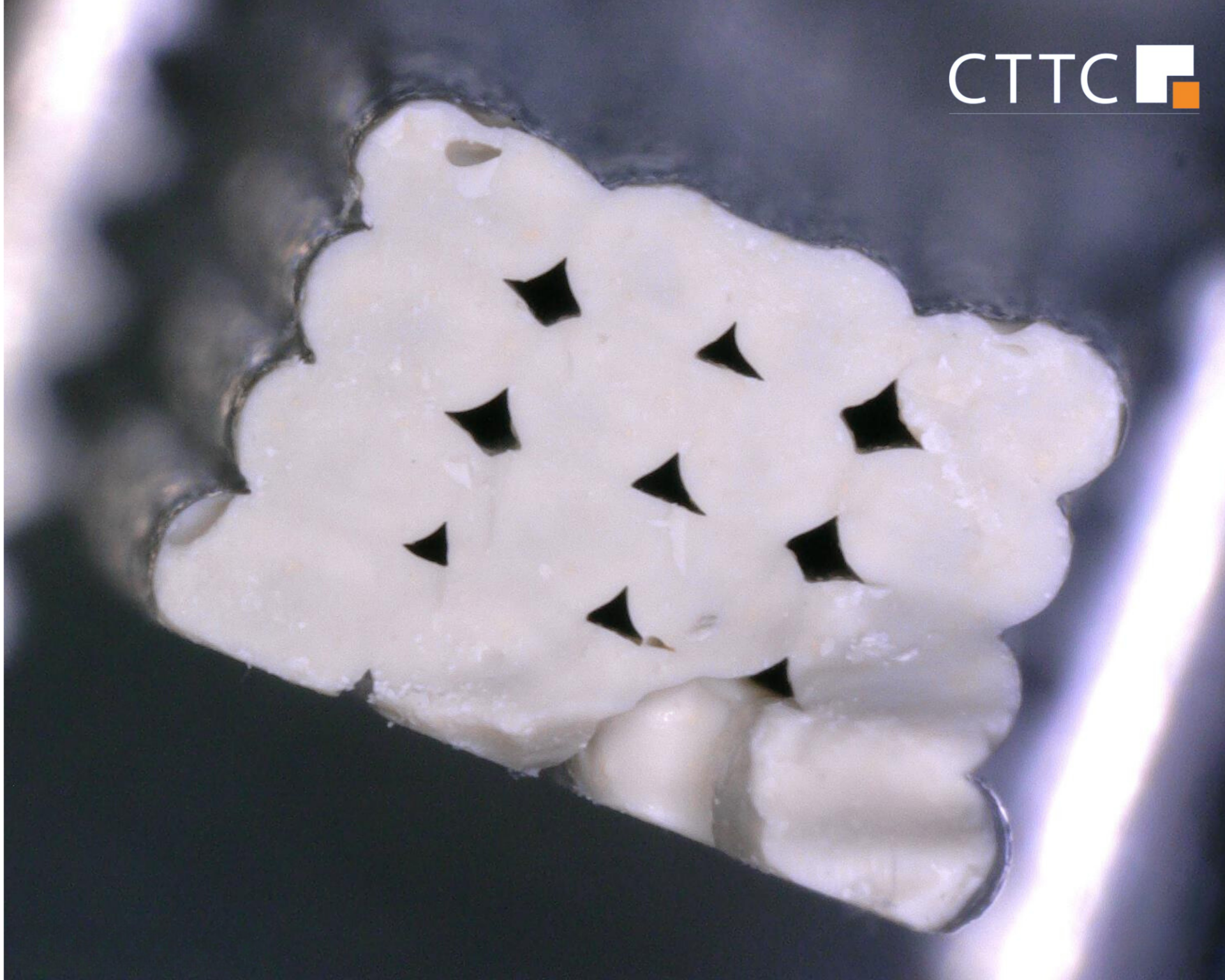
The project to date
To date, the efforts made as part of the CERAGREEN 3D project have led to the development of an alumina-based ceramic feedstock, printable from granules whose binder system is made exclusively from bio-based materials. This feedstock has a satisfactory loading rate, but it is still being optimised, in particular by adjusting its composition.
Printing parameters are also being optimised to increase resolution and improve the surface finish of the parts. With regard to the post-treatment of printed parts, CO2 SC debinding trials are being carried out using test samples. These trials will help determine the optimum parameters for eliminating and recovering as many biobased organic auxiliaries as possible. Particular attention will be paid both to preserving the initial geometry of the printed parts and to their mechanical strength before heat treatment. This heat treatment is also being optimised in order to achieve the highest possible densification of the parts without them showing any microstructural defects.
Depending on the results of the various material and process improvements described above, the development of other feedstocks will be considered, as well as the incorporation of other types of ceramic powders in order to diversify the material portfolio.
Thanks and Partnerships
The CTTC would like to thank the European Union and the Nouvelle-Aquitaine Region for their confidence and financial support. Without this support, a project of this scale would be difficult to carry out.
The CTTC would also like to thank the various partners who are taking part in the different projects in this programme
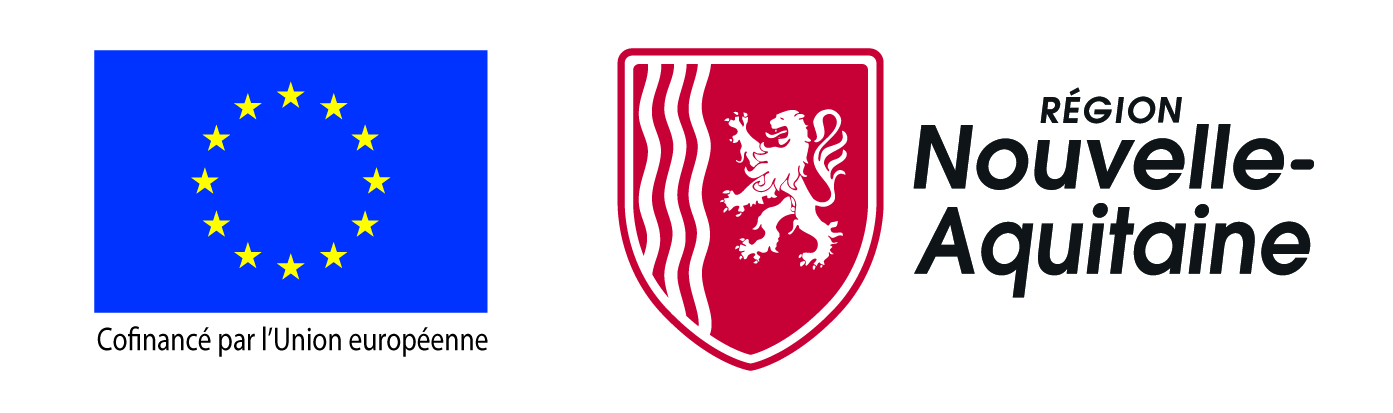