Technical ceramics: properties and applications in industry.
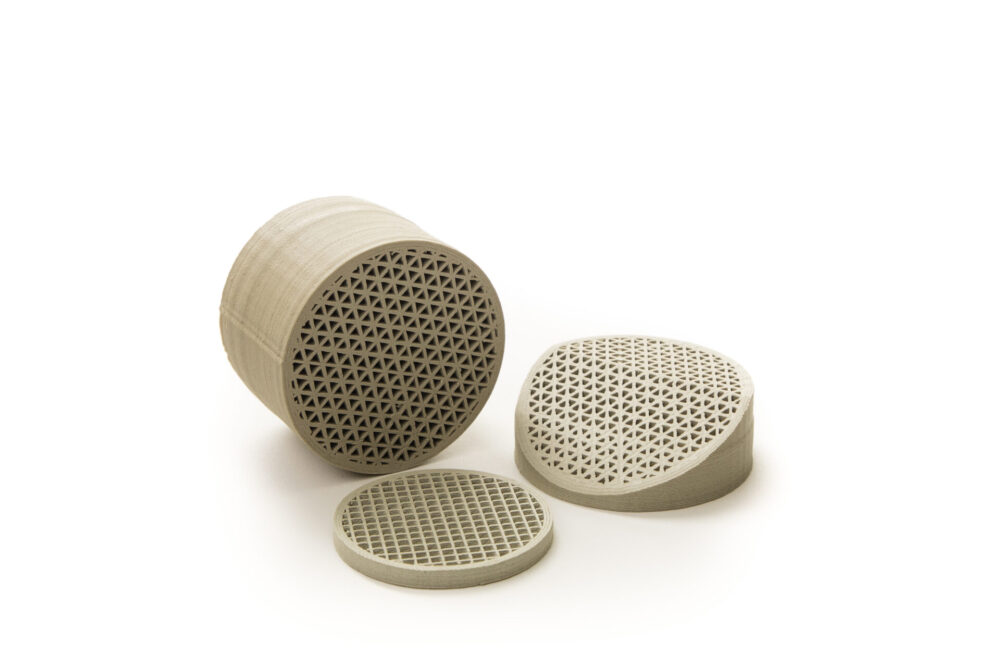
23 Oct 24
Articlesitems
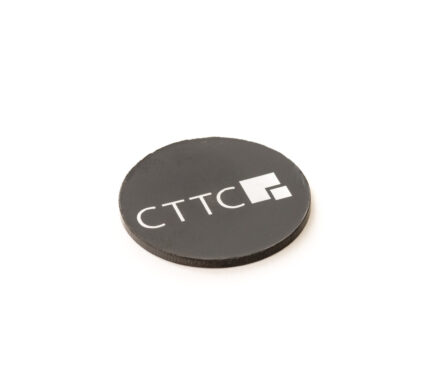
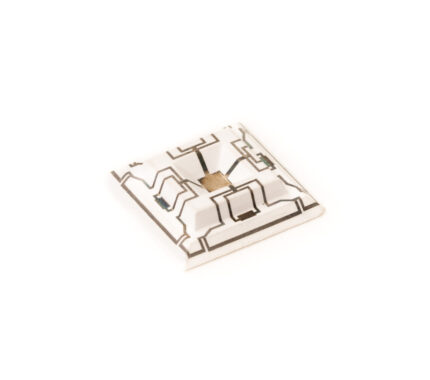
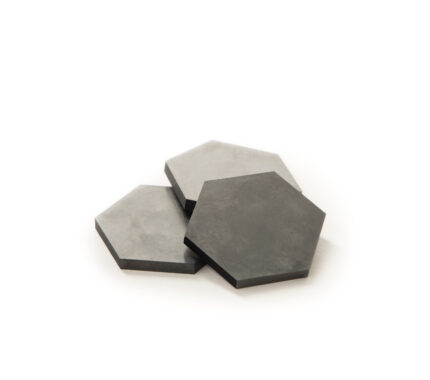
For over 40 years, the CTTC has mastered the processes involved in shaping technical ceramics. These materials, which are essential in many industrial sectors, are distinguished by their unique combination of physical and chemical properties. Because of this specificity, some industries are actively seeking out technical ceramics for demanding applications.
But what makes them so special? How are they manufactured? In what areas do industries use them?
This article explores the world of technical ceramics and their specific characteristics.
What are advanced ceramics?
Technical ceramics are inorganic, non-metallic materials specially designed for harsh environments. It is essential not to confuse them with traditional ceramics such as pottery, earthenware or porcelain. Technical ceramics are distinguished from the latter by their high performance under extreme conditions.
Specialists produce these materials from components such as alumina, silicon carbide, boron nitride, etc. Thanks to their high chemical inertness, low thermal conductivity and mechanical strength, technical ceramics can withstand high temperatures. They survive where other materials suffer destruction or severe degradation. Applications range from electronic components to medical devices. They also include protective elements in the aerospace industry.
What sectors use technical ceramics?
Technical ceramics are generally used in a wide range of sectors. These sectors require extreme conditions.
Here are the main sectors in which technical ceramics are used:
The aerospace and defence industries use technical ceramics for their resistance to heat (thermal coatings). They also use it for its high mechanical strength (resistance to impact, loading, etc.).
Electronics: in this field, technical ceramics are used for their electrical insulation properties. They are used in particular in high-reliability electronic equipment.
The medical sector: technical ceramics are used to coat surgical devices. This is due to their chemical inertness and resistance to wear.
The energy industry uses technical ceramics as neutron absorbers and fissile fuel. The electrical industry uses them as very high voltage fuses.
The automotive industry uses technical ceramics to filter diesel particles. In some cases, they are also used as linings in engine cylinders (Formula 1).
How are technical ceramics made?
The manufacture of technical ceramics requires meticulousness and rigour at every stage of the process. Here are the main shaping methods:
Cold Isostatic Pressing: this method uses high pressure to uniformly compress the ceramic powder inserted into a deformable mould. This process produces dense, homogeneous compacts (cru), which is essential to ensure good densification during sintering, guaranteeing and obtaining the required properties (mechanical, thermal, electrical).
Ceramic Injection Molding: this technique involves injecting a molten ceramic paste under pressure into a mould, which takes the shape of the part once it has cooled. The raw parts are then heat-treated to densify them. This process is particularly suitable for large production runs, provided that the geometry of the part can be adapted to the manufacture of an injection mould.
Extrusion: this process (cold or hot) also uses a ceramic paste that is forced through a ‘die’ to give it a particular shape (e.g. tube, cylinder, bar). This process is suitable when the parts have a more or less complex ‘linear’ geometry. It offers the advantage of continuous production without having to remove the part from the mould.
Casting: this method is based on shaping parts from a more or less viscous suspension, which is poured into an open or closed mould, with or without additional pressure. The liquid in the suspension is evacuated, leaving only the solid component (shaped powder).
Machining: depending on the complexity of the part to be manufactured, or when very precise dimensional dimensions are required, the technique of choice is machining, which removes material from a sintered block using diamond tools…
Thermal spraying: when metal parts need to be protected from a harsh operating environment (high temperature, friction, impact, corrosion, etc.) they can be coated with ceramic deposits, by heating and spraying the ceramic powder to create an adherent and protective layer.
Aerosol Deposition Method: this is an emerging technology under development at the CTTC, enabling cold ceramic coatings to be produced, i.e. without the need to heat the powder or the substrate. This process produces very dense (>95% of the theoretical density of the material) and nanostructured coatings, giving them very high mechanical properties.
Why are technical ceramics so sought-after?
Technical ceramics have unique properties that often surpass those of traditional materials. These exceptional characteristics make it possible to meet high-performance requirements.
Some key properties:
Resistance to heat and corrosion: these materials can withstand temperatures in excess of 1,000°C. They can even reach 1,500°C without degrading. Their near chemical inertness makes them ideal for corrosive environments.
Lightness: technical ceramics are often lighter than metals. This means significant weight savings in sectors such as aeronautics and space. This factor is crucial for improving energy efficiency. It also helps to reduce greenhouse gas emissions.
Hardness and wear resistance: the hardness of advanced ceramics far exceeds that of metals. This makes them ideal for applications such as cutting tools and components subject to intense friction.
Electrical and magnetic properties: some advanced ceramics are used as electrical insulators, while others exploit their magnetic properties. This enables them to be used in devices such as electric motors, transformers and sensors.
How much do technical ceramics cost?
The cost of technical ceramics can vary according to a number of factors, including the nature of the materials used, the complexity of the manufacturing process and production volumes. In general, these materials are offered at a higher price than traditional metals or polymers. However, their durability and superior performance justify this cost.
Innovation and research in technical ceramics
The field of technical ceramics is constantly progressing, with numerous research projects and innovations aimed at improving performance, making geometries more complex and broadening the range of applications. These include
- Ultra High Temperature Ceramics (UHTC)
- Ceramic Matrix Composites (CMC)
- 3D printed ceramics
In conclusion, technical ceramics are an essential asset for many industries looking for an alternative to traditional materials.
As a technical centre, the CTTC plays a central role in the research and development of these materials.
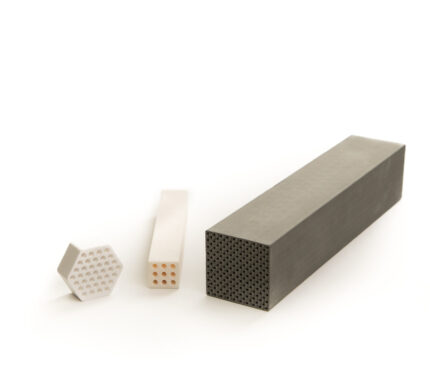
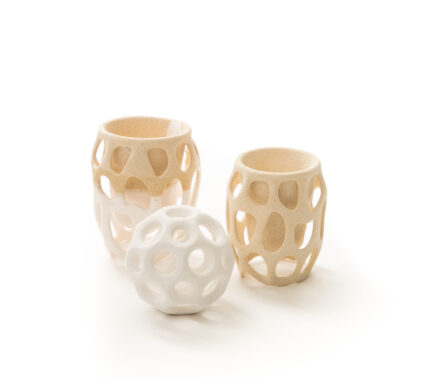
